You will find air compressors at any gas station or service station. They serve not only for pumping the wheels of vehicles, various pneumatic tools, jacks, spray guns are also connected to them. Probably everyone dreams of having such a tool in a workshop or garage. In our article we will tell you how to make an air compressor with your own hands from improvised means.
Content:
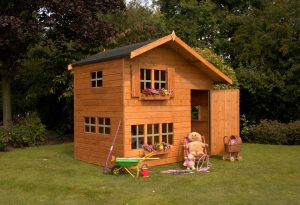
Materials for manufacturing
To make an air compressor you will need:
- gas cylinder for accumulating compressed air (receiver);
- wheels from an old cart;
- compressor of a truck, tractor or bus (in the example - ZIL-130);
- motor from a 220 V washing machine with a power of 300 W with a pulley;
- a pulley with an adapter for a compressor with a ratio of 13: 1 with a motor pulley;
- metal profile and round pipes;
- metal corner;
- plastic pipes;
- valves;
- tee, corners, flexible eyeliner;
- welding machine;
- Bulgarian;
- drill;
- fixing bolts, nuts, washers;
- automation for the compressor (other names - pressure switch, pressure switch) for 220 V;
- hose with a gun with a pressure gauge;
- expansion oil tank with tube and branch pipe;
- jar and sponge for the air filter.
Step 1. Create a Compressor Base
The compressor used in the example gives an output of ≈90 liters of air per minute, so a conventional gas cylinder as a receiver will be enough for operation and quick pumping.
We weld the wheels from the old trolley to the cylinder.
From a piece of metal pipe we make a leg.

We weld a metal handle from a profile and round pipe around the entire perimeter of the cylinder. The handle should be hollow inside and sealed - it will be used to cool hot air before pumping it into the receiver.
We weld a rectangular base from metal corners for attaching the main compressor units and weld it to the cylinder.

Step 2. Installing the units on the base
We drill mounting holes in the necessary places and install the electric motor on the base.

Next to it, aligning the pulleys in the same plane, we install the compressor of the car.

Next, we set the automation, adjusting it to turn on at 4 and turn off at 6 atmospheres. We collect power supply to the engine.

To cool the compressor, install an expansion oil tank and connect it to the compressor crankcase.

Step 3. Assemble the air system
Install an air filter to purify the air supplied. In the example, it is made independently from a can. A regular foam rubber sponge was used as a filtering agent.

At the air outlet from the compressor, we install the following assembly: angle - tee - angle and connect it to the radiator handle, which we welded in step 1. We connect the pressure relief valve from the line to the tee on the flexible connection.

On the reverse side of the handle from the corners and pipes, we assemble a structure for supplying air through the check valve to the receiver.

Step 4. Testing
We put the belt on the pulleys and turn on the power supply.

Having pumped up pressure to 6 atmospheres, the compressor turns off. Now you can connect any pneumatic nozzles to it.
ZIL compressor + motor from a washing machine
DIY air compressor: idea + video