For wiring electrical wiring use special devices called junction (junction) boxes. Their installation completely eliminates the possibility of bare cores coming out. The connection of wires inside the junction box is allowed only by welding, crimping and using special clamping devices.
Content:
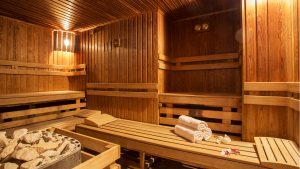
Purpose of junction boxes
How to choose an electric underfloor heating: comfort and reliability of autonomous heating
When laying electrical wiring, it is bred evenly from the shield to all rooms. In each of them, the wires branch out again and go to the end points of consumption: sockets, switches, lamps, etc. Junction boxes are installed at the nodal points - hollow structures designed to hide the wiring points. They are embedded in the wall 10-30 cm from the ceiling or left outside in the form of overhead devices.
The main purpose of such structures is to protect the joints from contact with combustible materials, physical damage, dust and moisture. In addition, junction boxes also perform an aesthetic role, covering soldering points or terminals that are not very aesthetic.
According to GOST R 50571.15-97, for access to the contents, such structures are equipped with lids or doors. Holes on the sides are for the output of wires. Immuring them without the possibility of free opening is prohibited. Even when mounting the box into the wall, its lid must be on the surface and open quickly and effortlessly. Sometimes junction boxes may contain already built-in terminals.
Products intended for internal wiring must have a protection level of IP20-30 and be made of polystyrene, polypropylene. The degree of protection of junction boxes mounted in hazardous areas is IP44. Structures installed outdoors are made of weather-resistant materials and have sealing seams.
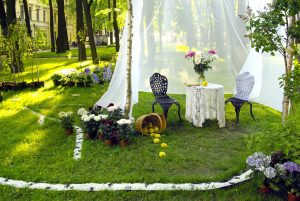
Box mounting
The place of its installation must be considered. After all, it should be quickly accessible. When mounting the box into the wall, a hole is prepared for it in the form of a recess. Then it is fastened with a solution of alabaster.
Strobs are being prepared for the supply of wires in the walls. All cores are laid in protective plastic or metal pipes. At the same time, they make channels for the sockets. All cores for safety must be marked. The cable coming directly from the shield is indicated by the word "input". It should have 2-3 cores and a cross section of 4 mm2.
1.5 mm conductors are used for lighting2, for 2.5 mm sockets2. When drawing up the wire connection diagram in the junction box, the phase should go to the phase (white wires), grounding, respectively, only to ground (light green wires), and zero only to zero (blue wires).
When laying the wires in the junction box, a small distance (allowance) of about 1 cm is left between them. When using any of the methods of connecting the cores, they must be insulated with plastic caps or ordinary electrical tape.
When diagnosing the assembled network, they connect the most powerful device and check if heating has appeared. If this happens, the junction box is disassembled and a connection with an insufficient contact area is looked for. It is also possible that conductors of insufficient cross section were used. In this case, they are replaced.
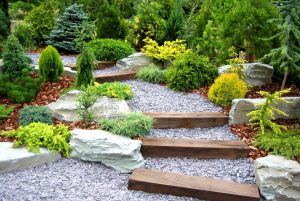
Connection methods
When choosing one or another connection method, you should first of all focus on the expected load on the network. According to the requirements of the PES, the installation of any types of electrical mains in a junction box can be carried out in three main ways.
The most commonly used welding and crimping. Connection by means of special screw or bolt clamps is also allowed. At the same time, their size must exactly match the cross section of the wires and the number of cores.
Welding
The welded method is suitable only for pairing wires made of homogeneous metals. It belongs to one of the most reliable connection methods. Unlike twists or even bolted connections, there is no contact resistance in it, which minimizes the likelihood of overheating of the contact and its short circuit.
This method is fundamentally different from soldering - melting between the wires of the intermediate material (most often tin-lead solder). When welding, the intermediate metal is not used. Produced only melting of contacting parts, as a result of which the wires turn almost into a single whole.
Adhesions due to the presence of a third, looser material, are able to weaken over time. Plus, at the joints, due to the difference in composition, destructive chemical reactions occur. Therefore, for the connection of wires inside the junction box by melting, according to PES, welding is required.
- To carry out the work, minimal skills are enough. In everyday life, for these purposes, spot or arc welding is most often used, which is performed on graphite (for copper) or carbon electrodes.
- It is better for beginner welders to use a machine with a constant current voltage of 12-32 watts. Experienced installers prefer to work with more powerful units with variable current
- The 5-6 cm ends of the wires are pre-stripped and then twisted. At the same time, 5-6 centimeters of the core should remain without twisting. They must be pressed tightly against each other. To form a molten ball, when mating three or more strands, only a couple of ends are left, the rest are cut off
- Even the twist is crimped with ordinary pliers or a clamp
- Melting is performed on top of the twist for 2-3 seconds. To do this, grounding from the welding inverter is connected to its upper part.
- If the current strength in the device is chosen correctly, the arc should turn out to be stable. Sticking of the electrodes does not occur.
- For welding a pair of copper wires with a cross section of 1.5 mm2 70 A is enough, for three cores 90 A. If they have a larger cross section of 2.5 mm2, the current strength will need to be increased to 80-100 A
Crimping
The most durable and reliable way to connect wires in a junction box is to connect using sleeves, followed by crimping (crimping). It provides perfect contact and increased mating strength.
It can be used for different types of wires, both copper and aluminum of different sections. But most often a similar method is used for medium and high currents. A similar method is widely used even on an industrial scale for crimping wires on high-voltage lines or substations.
Technically, this method is quite simple:
- When choosing sleeves, the material matching rule is used. According to the requirements of the arrangement of electrical installations, copper wires should be crimped only with copper sleeves, and aluminum wires with aluminum sleeves, respectively. To pair conductors made of different types of materials, use combined copper-aluminum types of sleeves
- For stranded wires, special insulated lugs must be purchased
- The stripped ends of the wires are inserted into the sleeve prepared in advance.
- Then it is pressed with press tongs. For sleeves of small diameter, it is more convenient to use a tool with curly jaws. If the sleeves have a larger cross section (from 12 mm2), special mechanical tongs with hydraulic drive are used
- In order to avoid damage to the cores, especially fragile aluminum ones, it is not necessary to press too hard and be zealous
- The last step is isolation. You can use electrical tape or heat shrink tubing for it.
Use of screw or bolt terminals
The simplest way, in which the wires are placed between the bolts and nuts. It is suitable both for connecting copper or aluminum wires in a junction box, and for pairing conductors made of different materials, that is, connecting copper with aluminum.
As you know, these materials are not galvanically compatible. When they are connected directly, you will get a mini-battery, which over time will simply oxidize during the electrolysis reaction. As a result, the contact will loosen, it will heat up and, as a result, the wire will burn or short circuit. In order to avoid the oxidation process, a different material must be laid between the copper and aluminum conductors, in this case a steel washer.
To do this, the end of each core is twisted into a ring so that the eye is completely closed by the washer and does not come into contact with the adjacent conductor. It should be located so that the ring is pulled inward.
The industry produces special clamps for joining copper and aluminum, containing a paste that inhibits the oxidation process. The use of galvanized bolts and washers is prohibited. Indeed, for the conjugation of different materials, it is allowed to use metals with a small electrochemical potential.
Since bolt and screw assemblies are quite bulky, in recent years they have been replaced by more compact terminal blocks equipped with nut clamps. Outwardly, these devices look like tubes equipped with threaded holes on both sides for inserting screws. For stranded wires, special brass lugs are available.Cores with a large cross section are enclosed in bolted terminal blocks equipped with an opening cover.
The method of using conventional screw or bolt clamps has another significant disadvantage. The contacts in them loosen over time, so the screws and bolts needs to be pressed periodically.. When connected with terminals, the nuts do not loosen even with time, therefore they do not require periodic tightening. The probability of their closing is minimal.
Terminals
How to plaster walls with your own hands: instructions for beginners (Photo & Video) + Reviews
The use of terminals fully meets the requirements of the PUE. However, their use is justified only if the junction box is equipped with ready-made pads. In addition, this method is more suitable for laying multi-core cables in a box - it is more difficult to compress single-core wires without damage, and together with the terminal they will take up a lot of space.
It will be problematic to separate the cables to the sides in this case. The ideal option for using terminal blocks is a wired connection with a screw, without crimp terminals.
You can see clearly the process of connecting the cores in the junction box in the following video. It details each of the recommended types of electrical wire connections in a junction box:
VIDEO: All types of wire connections. How to connect a wire.
Connection of wires in a junction box: types of connections and their application