Aluminum is a fairly common metal widely used in the national economy. Its alloys are mainly used, but sometimes it is used in almost pure form. We will tell you how solder aluminum at home.
Content:
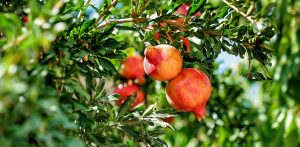
Why do soldering problems occur?
This metal has many advantages, in particular, lightness and flexibility. In addition, due to the oxide film formed on its surface, the metal is practically neutral and does not react with aggressive media or food products.
However, it is precisely this property of the metal that is a problem in cases where it is necessary to connect several aluminum parts using soldering.
Most often, aluminum is used as a material for the manufacture of various radiators: heating systems, cooling electronic components, automotive fluids, etc. Such use is due to the low heat capacity and high thermal conductivity of the metal.
Despite the rather low chemical activity, time and temperature do their job and cracks appear in the cases of aluminum radiators, which are quite problematic to repair.
Microcracks that occur in radiators may even be invisible to the human eye, but a sufficiently large amount of liquid can leave them, which will have to be regularly added to the cooling system.
Repair of the cooling system is quite an expensive undertaking. Often, service centers or auto repair shops, without much effort, simply change the entire radiator instead of fixing it by soldering the hole.
You can fix the hole yourself in two ways: soldering or cold welding. At the same time, in both cases, one will have to face one serious problem.
When aluminum interacts with air, it immediately oxidizes, and its surface is covered with a thin film of oxide.
Oxide has insulating properties and traditional materials used as solder are not able not only to connect two aluminum surfaces, but even to “stick” well to the surface that the oxide covers.
That is why soldering aluminum is very, very difficult.
Soldering with a conventional soldering iron does not give the desired results. It can even be said that it does not give any results, because even when using special fluxes for soldering, instead of an even soldered seam, an uneven heap of solder is regularly obtained, which obviously does not have good contact with any of the soldered surfaces.
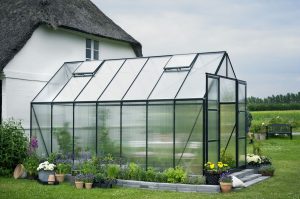
How soldering is done
For soldering aluminum, a specialized solder is used, able to resist the protective effect of the oxide film on the metal surface.
Several brands can act as such solder, for example, HTS-2000 or Castolin-192. Structurally, these solders are a tube of low-melting metal (zinc compounds are used), in the center of which a special flux for aluminum soldering is poured.
It is this flux that is used to dissolve a thin oxide film on the aluminum surface. In order to carry out the soldering correctly, it is necessary to ensure the temperature of the surfaces to be soldered is +480°C.
At lower temperatures, the solder metal will not be able to react with the oxide and decompose it into its constituents, thus allowing the solder material to make good contact with the surface.
In order to give the structural elements the required temperature, a conventional gas burner is used. For this purpose, you can use both a portable and a stationary gas burner.
You can get solder that allows you to solder aluminum in specialized stores that manufacture and sell various products from copper tubes and radiators. This may be, for example, a service center for the repair of refrigerators, etc.
Sometimes the search for the right solder can take quite a lot of time, since the problem is quite specific and the information of interest may not be everywhere. In extreme cases, you can use the services of any trading platform. This may be, for example, the same Avito network.
But it is best (if, of course, there is an opportunity to wait) to contact Aliexpress. There you can order any solder for aluminum of interest at an attractive price and fairly fast delivery times.
It is advisable before starting soldering, especially if it is done for the first time, to conduct a training soldering of the holes. To do this, in any unnecessary tube, several holes should be made that will need to be soldered.
Therefore, it is not necessary to choose low-power burners or a frankly low-quality product for heating the parts to be soldered.
The flames of such burners will be too narrow, it will not warm the edges of the seam well, and the soldering will take a very long time, since the solder will constantly try to drain from the soldering point, collect into balls, stick reluctantly to the metal, etc.
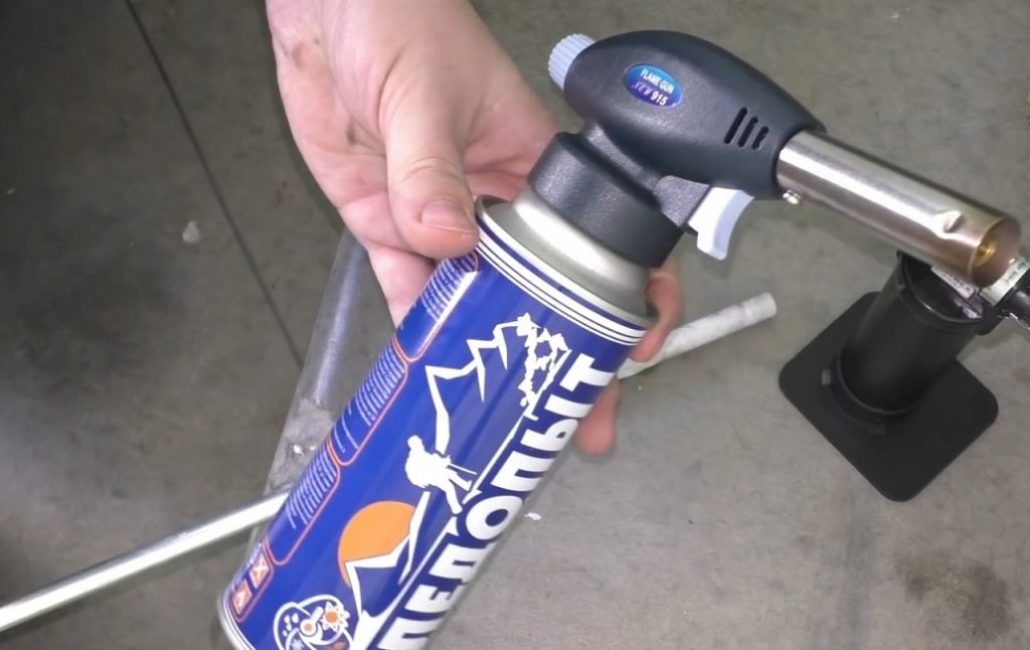
Soldering aluminum parts with low-power burners is very problematic, so it is better to use a burner nozzle on a cylinder
Its wide flame allows you to warm up in one pass not only soldered places, but also metal at a certain distance from them.
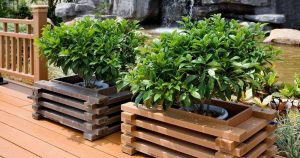
Soldering sequence
In order to solder two aluminum parts, you must do the following:
Using this method, you can not only solder aluminum products, but also solder together sheet aluminum.
Similar to the previously considered case, at first the all-round heating of the surfaces to be soldered is carried out, and then introducing a solder-flux tube into the burner flame at the point of contact between the two parts.
As a result, it should look something like this:
- The strength of soldering in this way is very high, and the connection is reliable.
- Breaking a seam is very, very difficult.
Let's take an example of how to solder two tubes. At the beginning, they are placed opposite each other and aligned.
Then everything happens according to the classical scheme: the ends of both tubes are heated to a depth of at least 3 cm. Next, they concentrate the fire on the seam and simply bring the solder to the seam.
The solder spreads quickly and the tubes are immediately soldered.
Solder completely fills the seam in a circle. At the same time, thanks to the flux, which spreads exclusively along the seam, the solder does not get inside the tube and does not clog it. This makes the seam very strong. The tube bends quite easily, but the seam remains intact.
Zinc solder has a very high fluidity; it fills the groove completely, making the connection airtight. Similarly, any aluminum structures of any diameter can be soldered.
In such cases, a complete element element replacement may be required. But that's a completely different story.
Conclusion
The very method of soldering using zinc solder in the form of a tube with flux inside is a working option, in addition, it can be classified as a budget one.
The cost of a 50 cm tube with flux is about 90 rubles. This is more than a good solution, against the backdrop of operations such as argon welding. Its cost can be several hundred, or even thousands of rubles.
A similar soldering method is often used in automotive workshops to repair radiators.
VIDEO: SOLDERING ALUMINUM. ARGON NOT NEEDED!
SOLDERING ALUMINUM. ARGON NOT NEEDED!
[Instruction] Soldering aluminum at home
podľa môjho názoru a skúseností, treba v mieste spájania vytvoriť malú ryhu pilníkom. Spájka sa potom roztecie a nebude vypadávať.