If you have roofing work at home or in the country, and sheet metal is chosen as the main material, then you simply cannot do without electric metal shears. Such a high-quality power tool is not cheap. We suggest you cut tin with an electric drill. Don't believe? Then read the article to the end. A little effort and a minimum of material costs - and you will have a drill attachment for cutting metal on your farm.
Content:
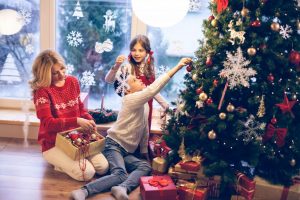
Materials for manufacturing
To make nasadcat on a drill for cutting metal, you will need:
- two bearings ø 50 mm;
- a shaft for them with a lock at one end and a shank for a drill chuck at the other;
- bearing ø 25 mm;
- shaft for a smaller bearing with a retainer;
- metal pipe with inner ø 50 mm;
- sheet steel 4 and 2 mm thick;
- bolts and nuts on M8;
- handle from grinder or perforator;
- welding machine;
- marker;
- Bulgarian;
- calipers;
- drill;
- vise;
- hammer;
- paint cans.
Step 1. Making an eccentric
We weld two shafts for bearings, aligning them with clamps with such an offset that the small bearing does not protrude beyond the large ones.
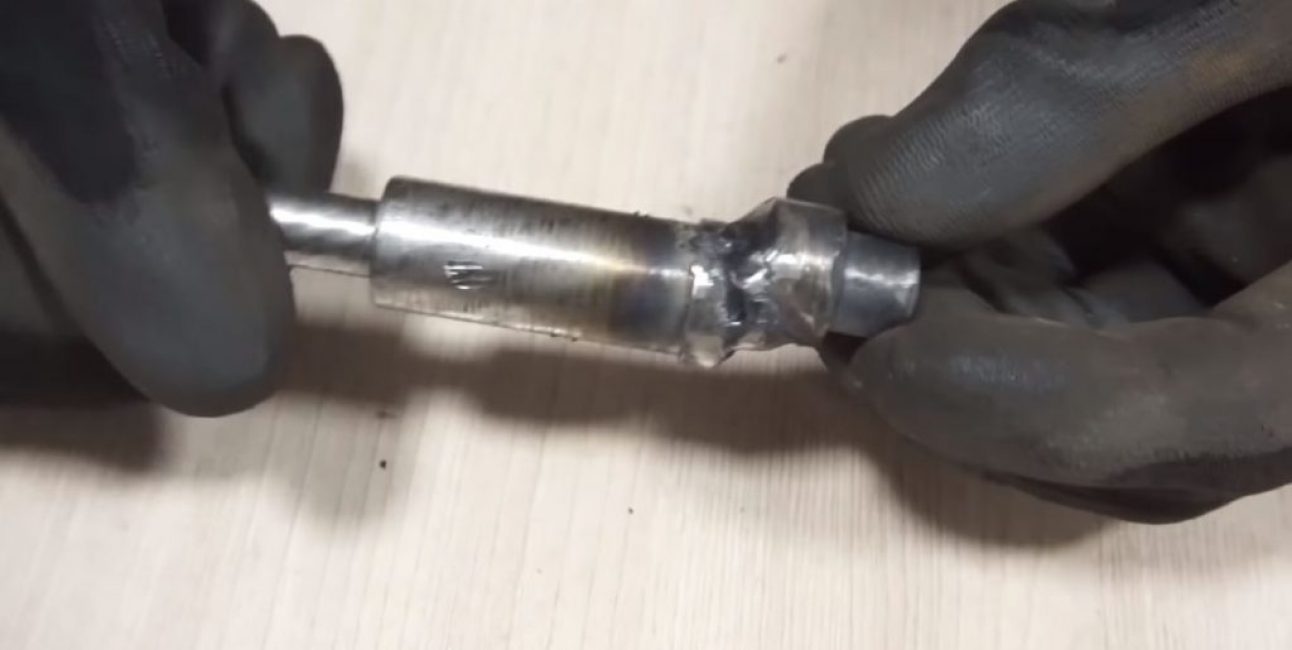
We cut off a piece of the required length from a metal pipe so that it covers the bearings.
We put on bearings and weld a small one to the shaft, and large ones to the shaft and the inside of the pipe.
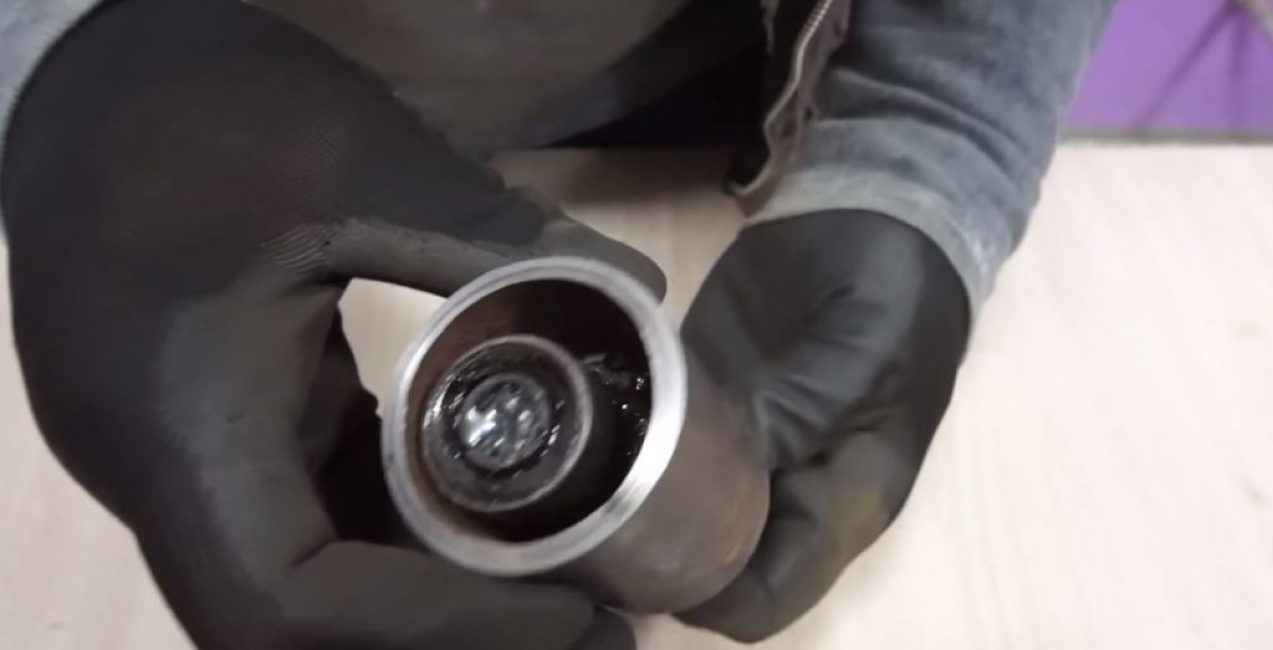
From a sheet of thin metal, cut out a plug on the pipe and spot-weld it. We grind the edges of the plug with a grinder.
We cut a rectangular hole in the center of the plug, deepening it into the pipe walls to the thickness of a small bearing.
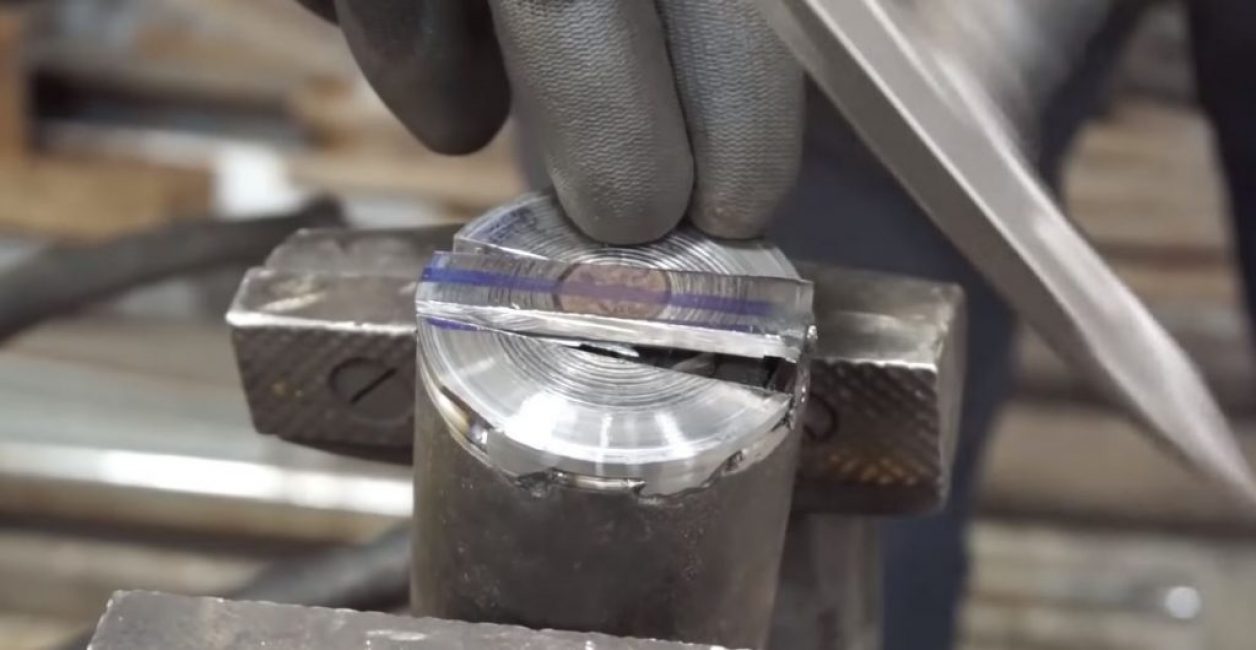
From a sheet of thin metal we cut out two eyes, which we weld along the edges of the rectangle cut out in the plug.
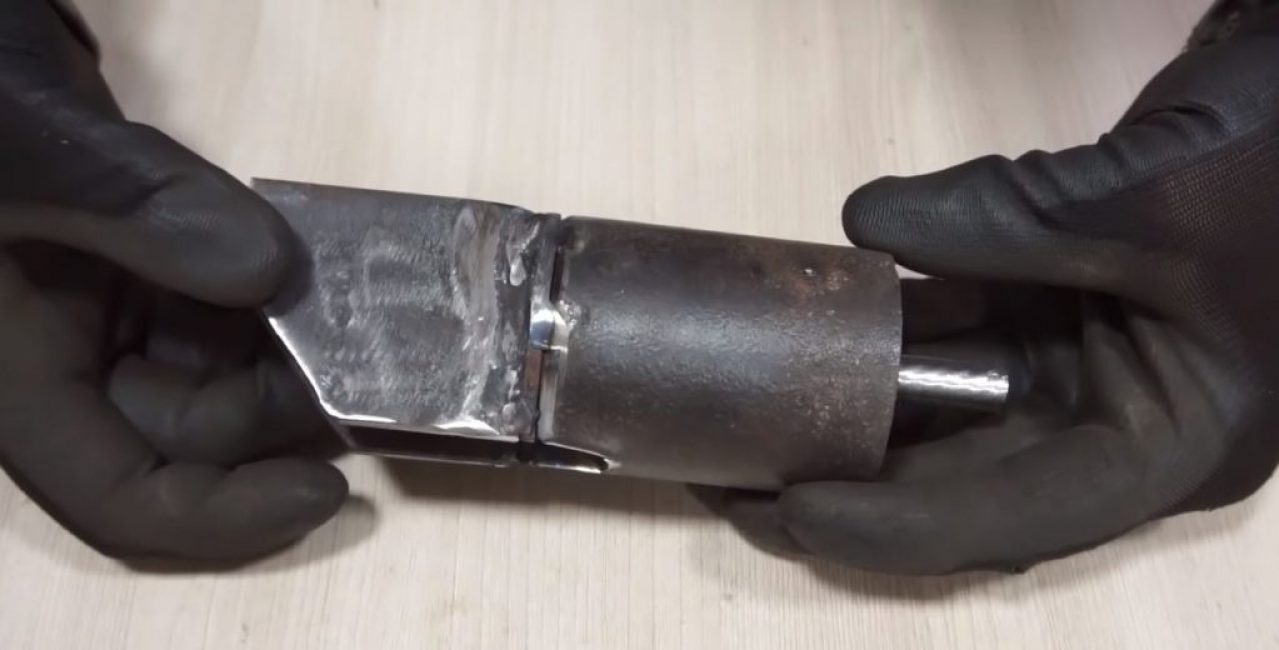
Step 2. We make and install knives
First, let's make a movable knife. From a sheet of thick metal, we cut out a blank for it of such a width that it easily goes through the slot on the plug into the pipe.
At the end of the workpiece in the center, we cut out a rectangle according to the diameter and thickness of the smaller bearing.
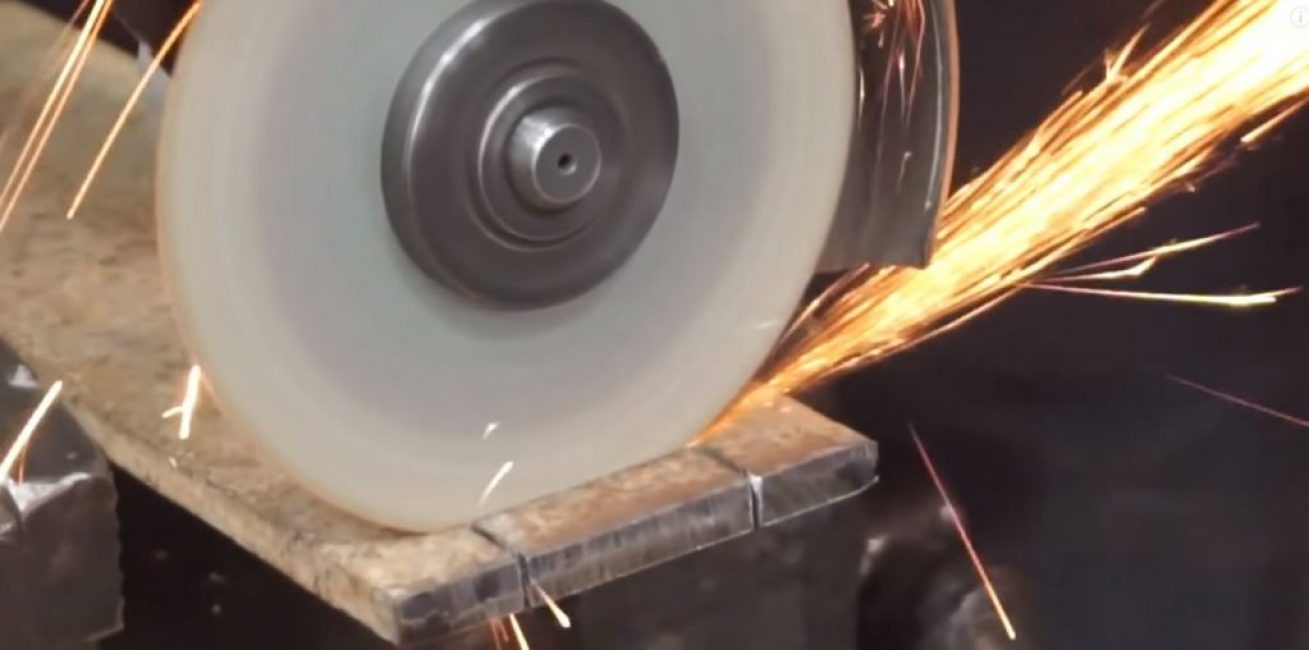
Let's try it on an eccentric. With a marker, we mark holes in the eyes for attaching knives and drill them.
We also outline and drill a hole in the movable knife.
We try on the knife in place, check its progress when the eccentric shaft rotates. Marker draw the shape of the knife.
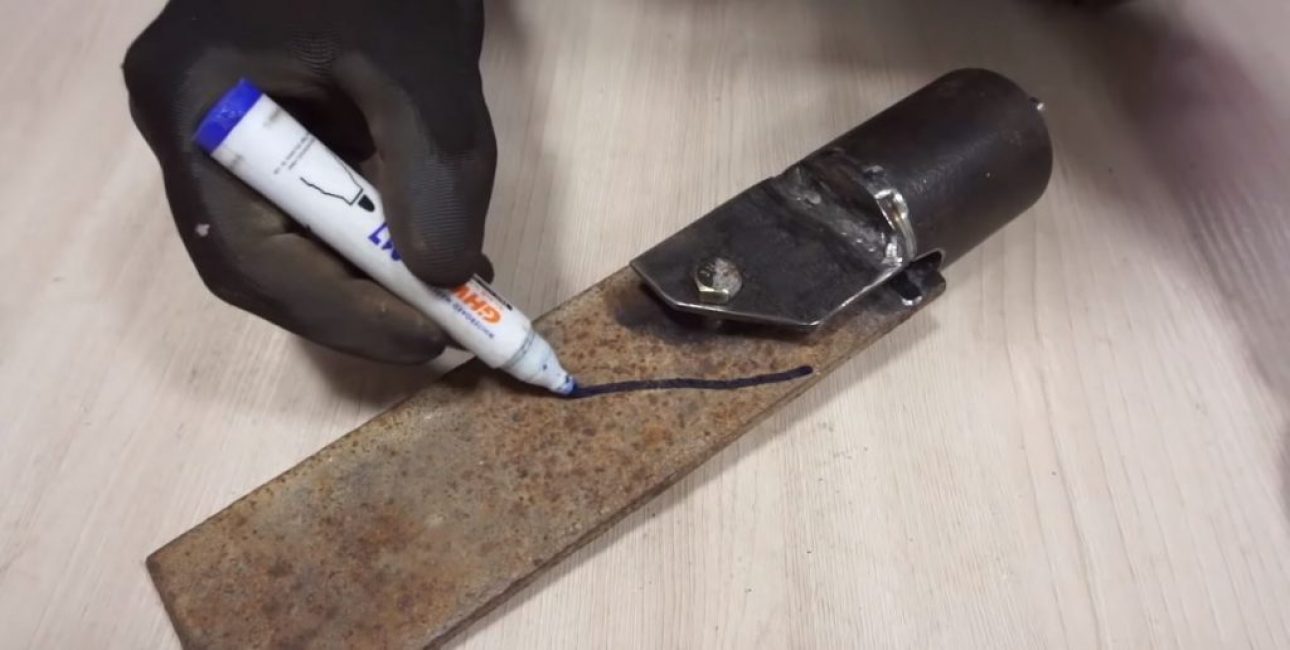
We cut the knife with a grinder and grind it.
Similarly, we cut and grind a fixed knife. We sharpen it.
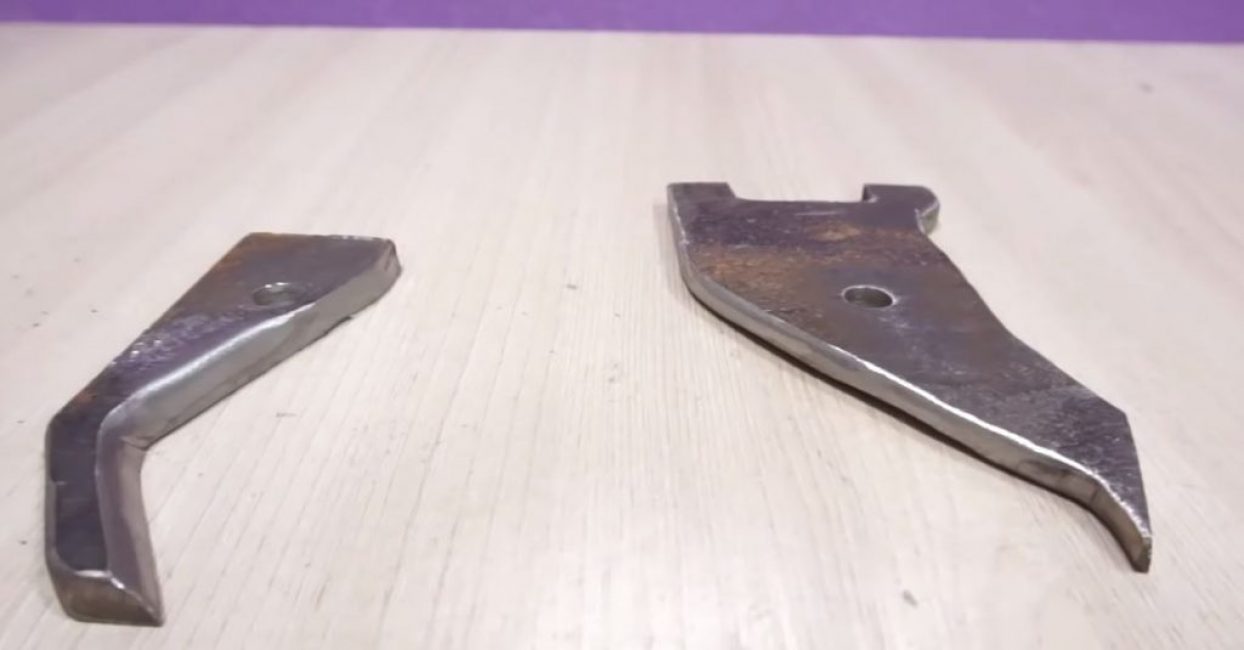
We harden knives (For how to harden metal, read the article “How to harden metal at home?“)
We install the knives in the eyes and fasten them with a bolt and nut.
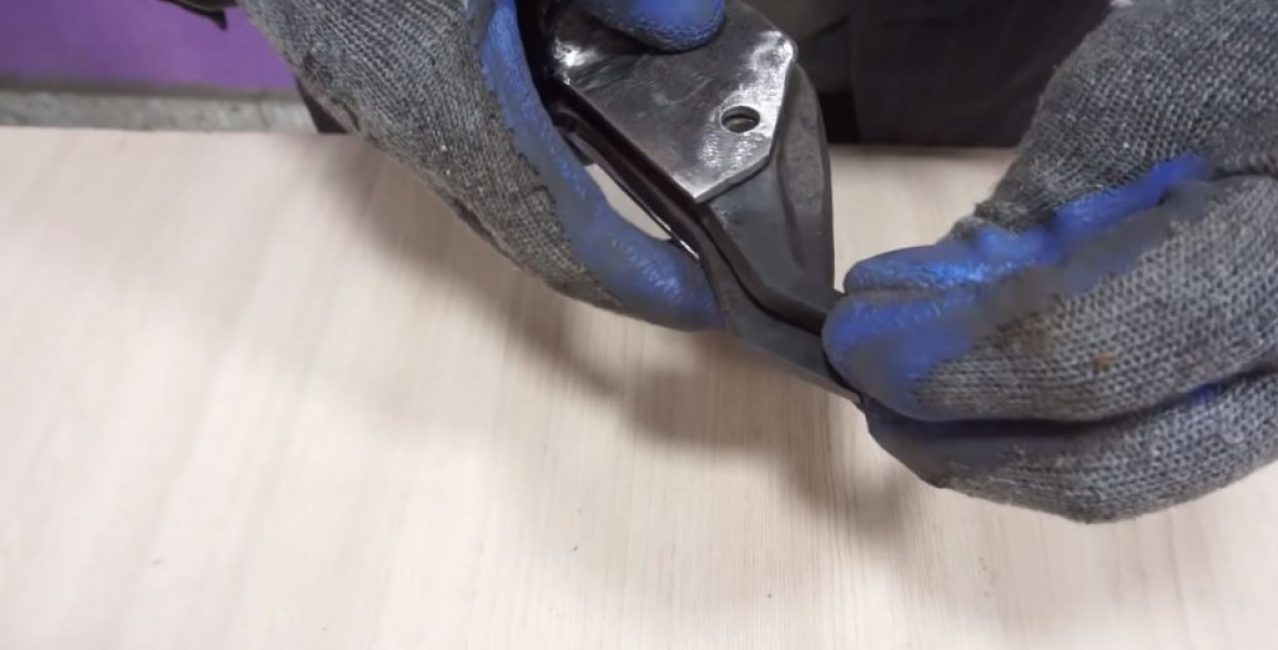
The fixed knife is welded to the eye.
Step 3. Attach the nozzle to the drill
From the pipe of the desired diameter, we cut off a piece of such a length that it is on the body of the drill at the place where the handle is attached.
We drill a hole in it and weld a nut so that the ring can be pressed against the body of the drill.
We cut out two strips from a sheet of thin metal to fasten the ring to the eccentric body.
We try everything assembled on a drill. With a hammer, we bend the strips accordingly and weld them, connecting the mounting ring with the eccentric.
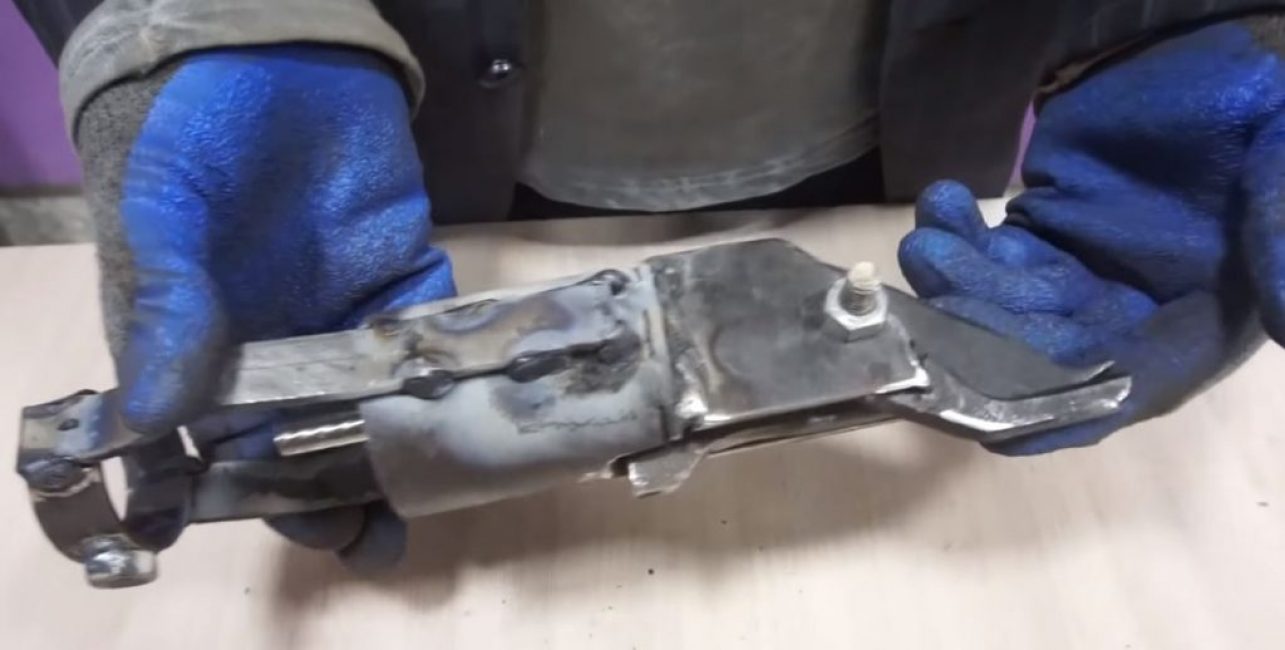
We weld a nut for attaching a handle from an old power tool to one of the strips in a place convenient for work.
We grind all the irregularities with a grinder and paint the scissors with spray paint.We install the handle - our unusual nozzle on the drill is ready.
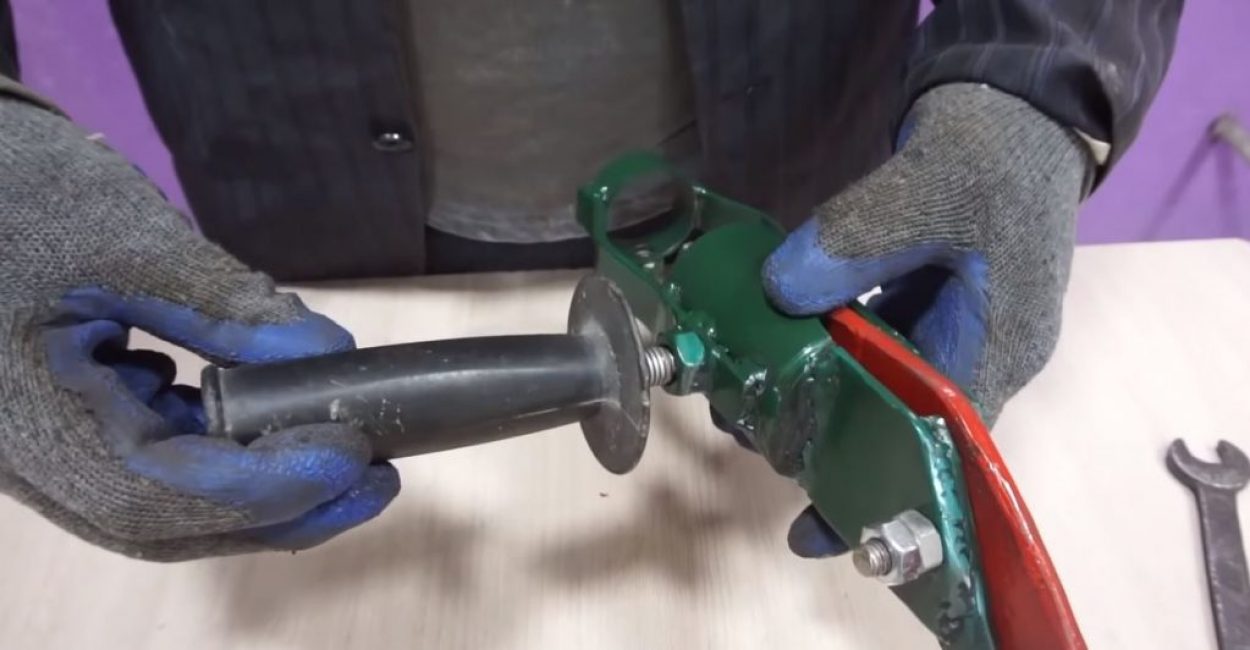
As you can see, our scissors easily and quickly cope with various sheets of metal.
Link to video:
Cutting sheets of metal with a drill
Nozzle for a drill for cutting metal | A tool that will speed up and simplify the process at times