Both professionals and beginners often have the question: “How is the welding of thin metal with an electrode carried out correctly?” Such welding is required when repairing washing machines, boilers, cars, etc. In order to weld products from thin sheet metal (less than 2 mm thick), you need to know some rules. For example, to weld 2 metal parts with a thickness of 1-2 mm, you need to take an electrode of the appropriate thickness (in this case, 2 mm). Moreover, it is necessary to reduce the welding current, approximately to 60 A, so as not to burn through the metal. The value of the welding current depends on the thickness of the metal.
Content:
Content:
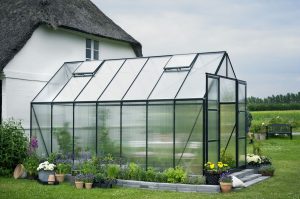
materials for work
In order to weld thin metal, you will need:
- 2 metal profiles;
- welding machine;
- electrode of appropriate thickness;
- protective mask and gloves;
- hammer.
Step 1
In order for the profiles not to move during the welding process, we fix them with a spot weld along the edges.
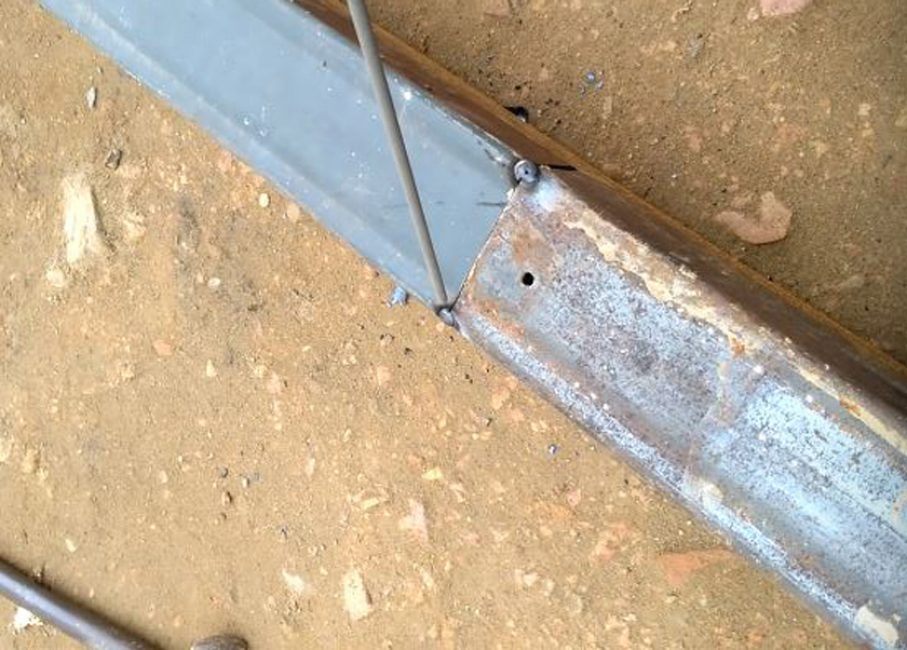
Step 2
It is very difficult to weld with a continuous seam on thin metal. You need to take small breaks. And so that you do not have gaps in the seam for metal, then after you have torn off the arc, you will need to return the electrode to the same place.
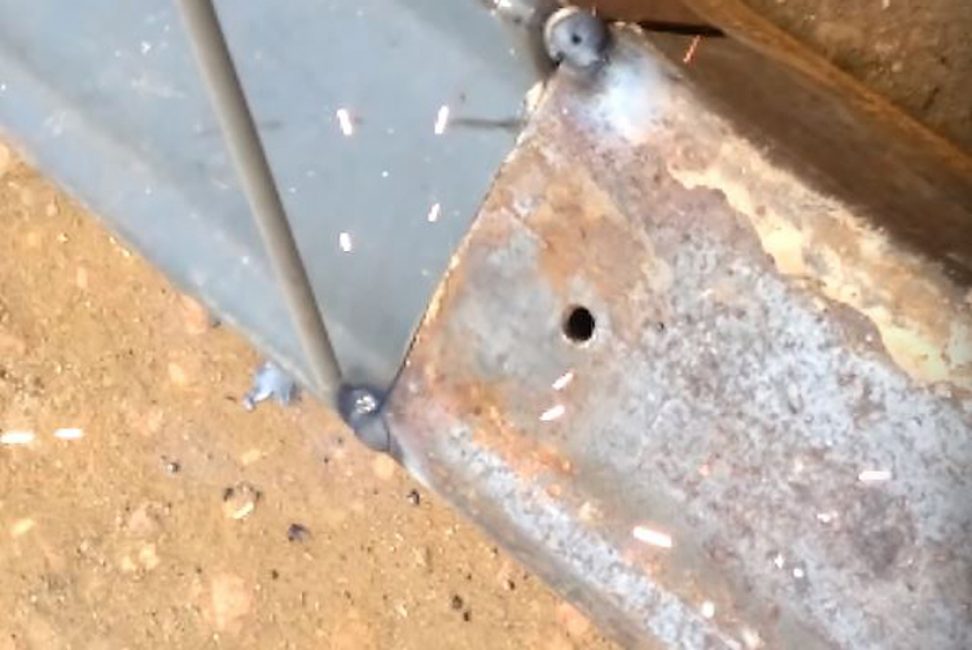
Step 3
It is important to have time to return the electrode to the place of welding before the metal crystallizes. Otherwise, you will be cooking on top of the slag. If this still happened, you need to stop the welding process, beat off the slag and continue the weld.
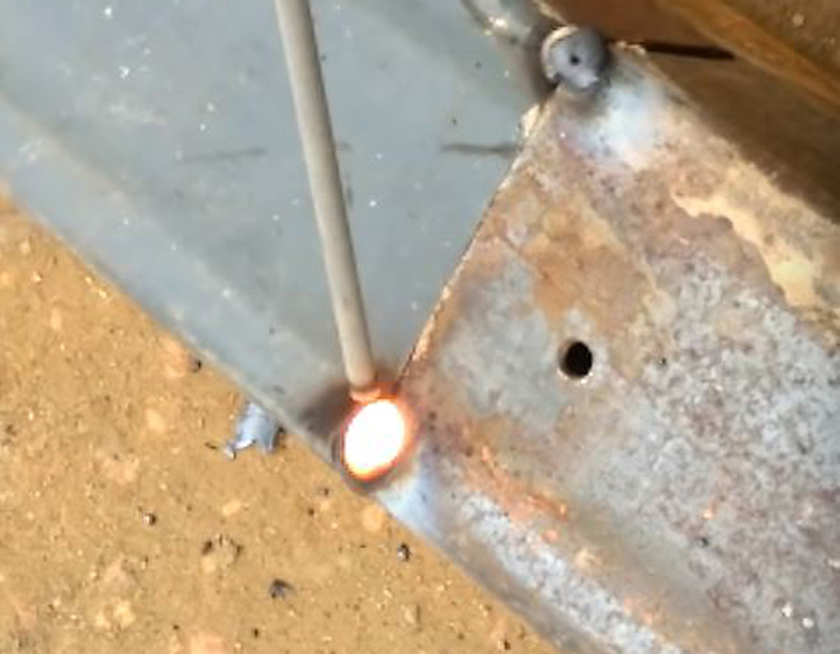
Step 4
Gradually, we slowly move along the junction of the profiles.
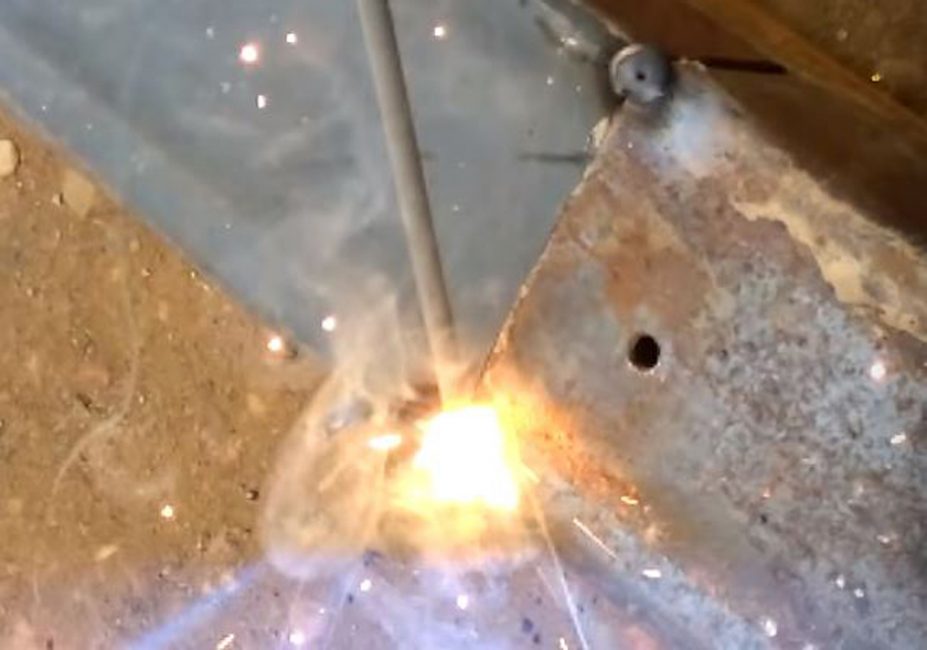
Step 5
So boil the entire joint to the end.
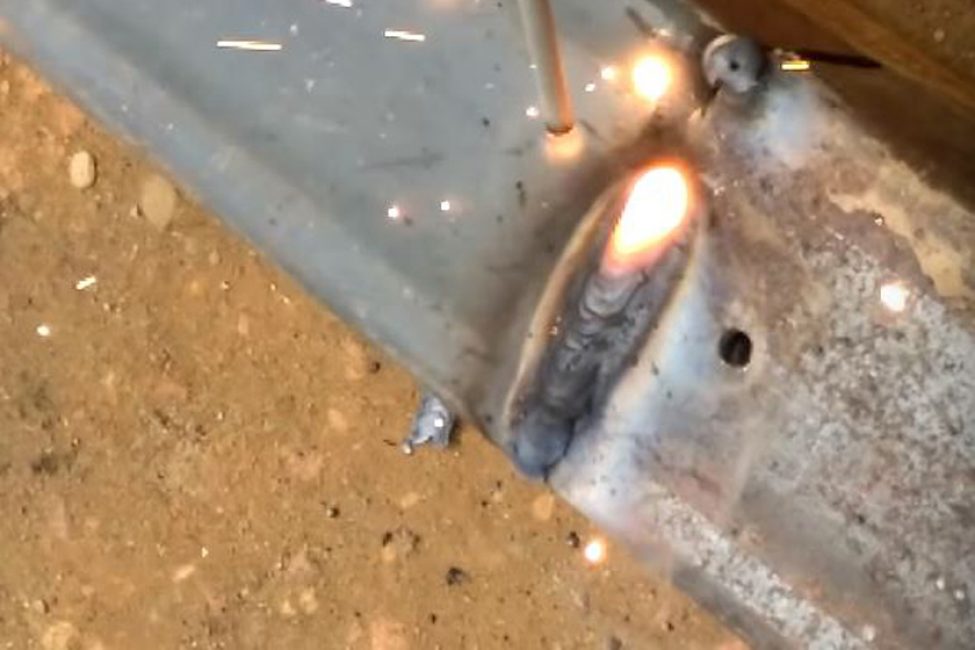
Step 6
As a result, we get such a seam.
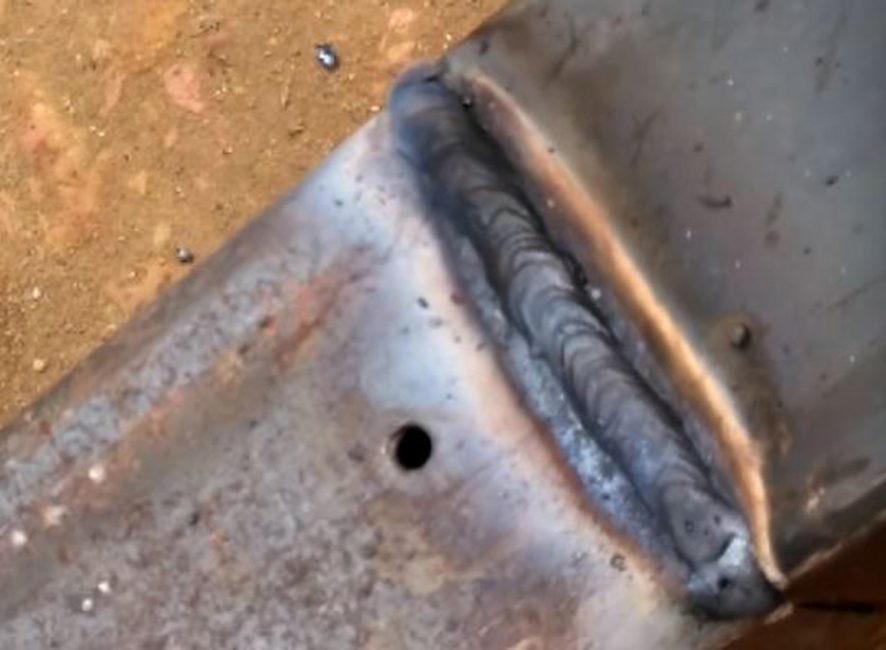
Step 7
We beat off the slag with a hammer.
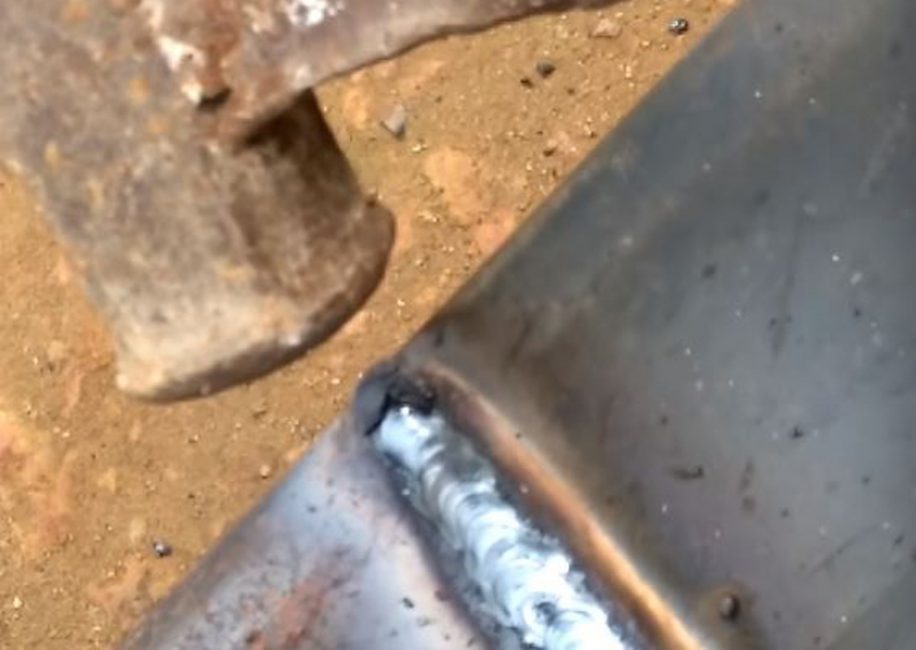
Step 8
Final result.
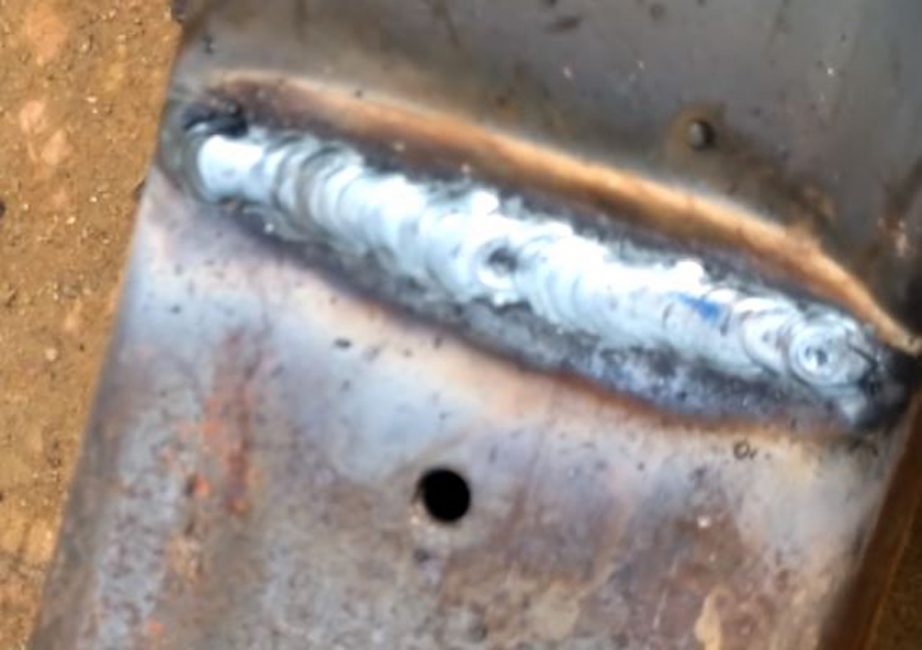
Video: How to weld thin metal by welding
How to weld thin metal by welding
How to weld thin metal with an electrode: tips for beginners and professionals ⚡⚡⚡