If you are not a fan of plastic pipes and are going to change water pipes at home or in the country in the near future, then you definitely cannot do without a pipe bender. Purchasing it in a store, especially if you are not going to deal with plumbing professionally in the future, is not economically profitable. There is an exit. In this article we will tell you how to make a pipe bender with your own hands at minimal cost.
Content:
![Powerful do-it-yourself wood saw [LIFE HACK]](https://iherb.bedbugus.biz/wp-content/uploads/2019/10/elektronozhovka-svoimi-rukami-300x169.jpg)
Materials for manufacturing
To make a pipe bender you will need:
- 8 bearings 303 series;
- channel 40x80 mm;
- metal corner 25 mm;
- Bulgarian;
- construction stud with thread ø18 mm;
- 6 large washers;
- 9 nuts for 18;
- welding machine;
- drill;
- thick steel sheet;
- pipe ø27 mm;
- nails;
- profile pipes 20x40 and 20x20 mm;
- mandrel.
Step 1. We prepare the basis for the pipe bender
From a channel with a size of 40x80 mm, we cut off a piece of the required length with a grinder.
We clean it from rust with a nozzle-brush.
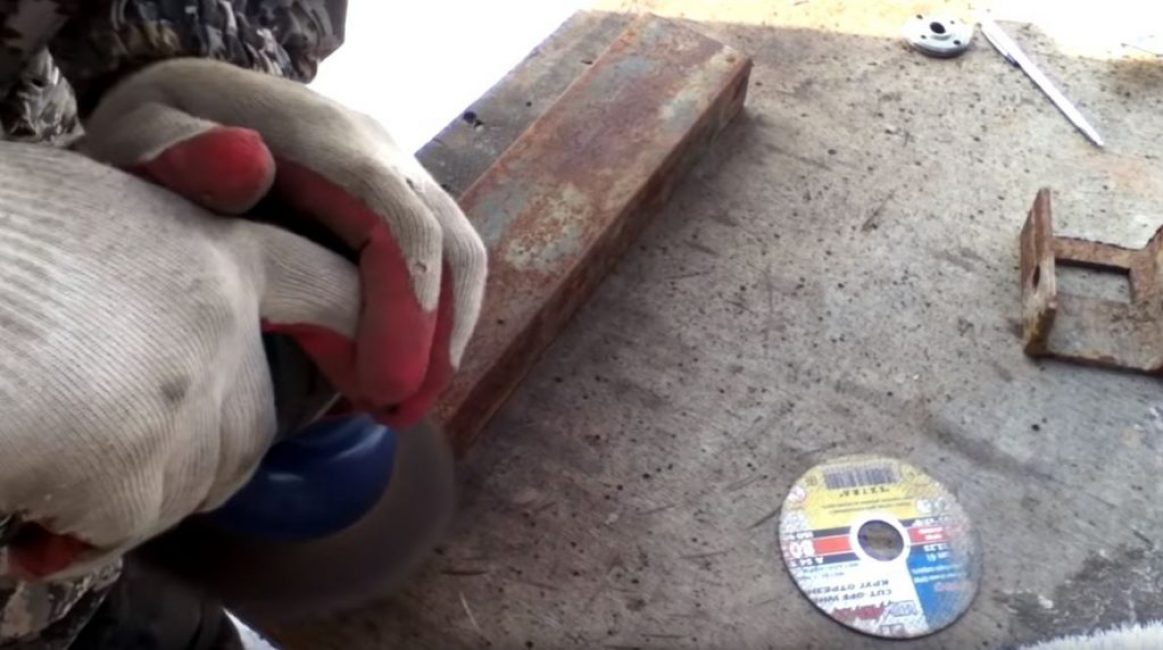
Step 2. Making rollers
From the construction stud we cut 3 segments. Two - for the manufacture of rollers, one - a movable carriage.
We remove the thread in the center of the segments with a grinder so that the bearings move freely.
Large 18 washers will serve as limiters for the rollers. So that they do not interfere with the rotation of the bearings, we will give them a slight taper with a mandrel and a hammer.
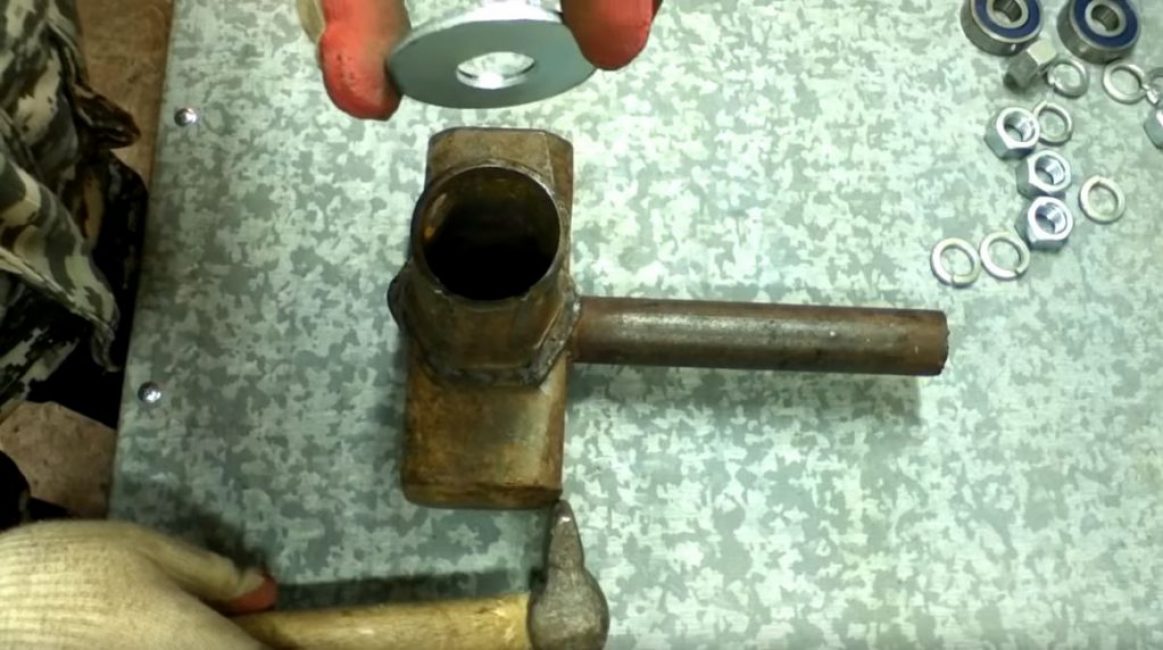
Sequentially we put a nut, a washer, three bearings on the stud, again a washer and clamp everything with a nut.
We grab the stud, nuts and washers by electric welding.
Cut off the protruding part of the stud. In total, we make two such designs.
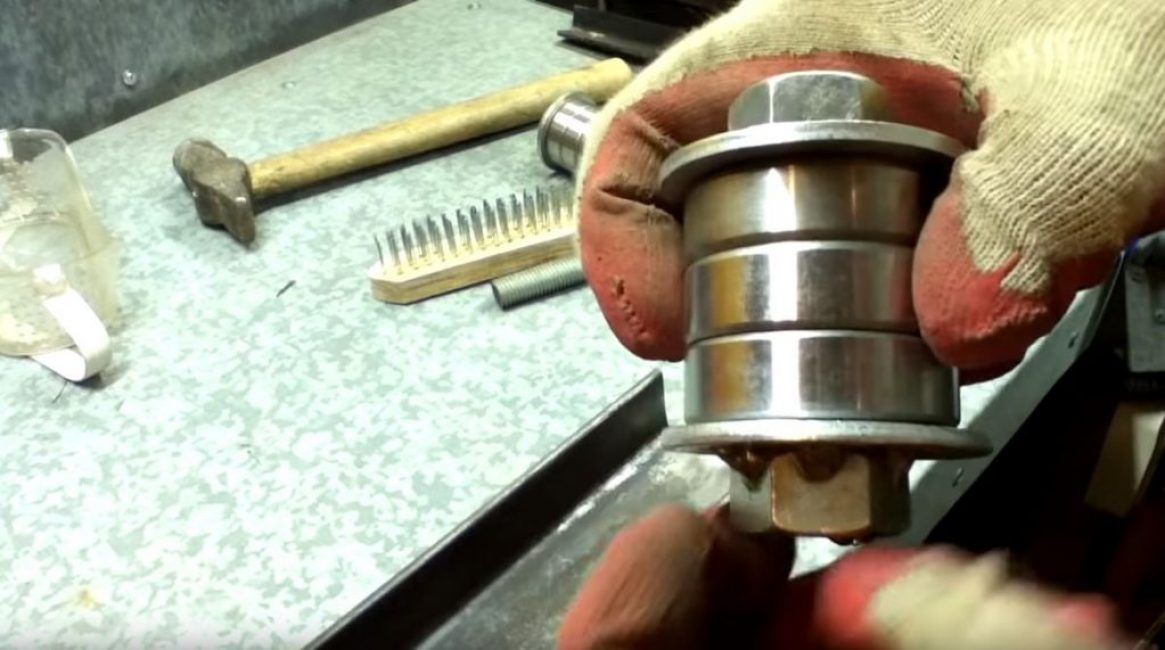
Step 3. Making a lifting and clamping mechanism
We cut four pieces 25 cm long from the metal corner. They will serve as guides for the pressure roller.
We weld them to the base of the channel, leaving a gap for the free movement of the stud.
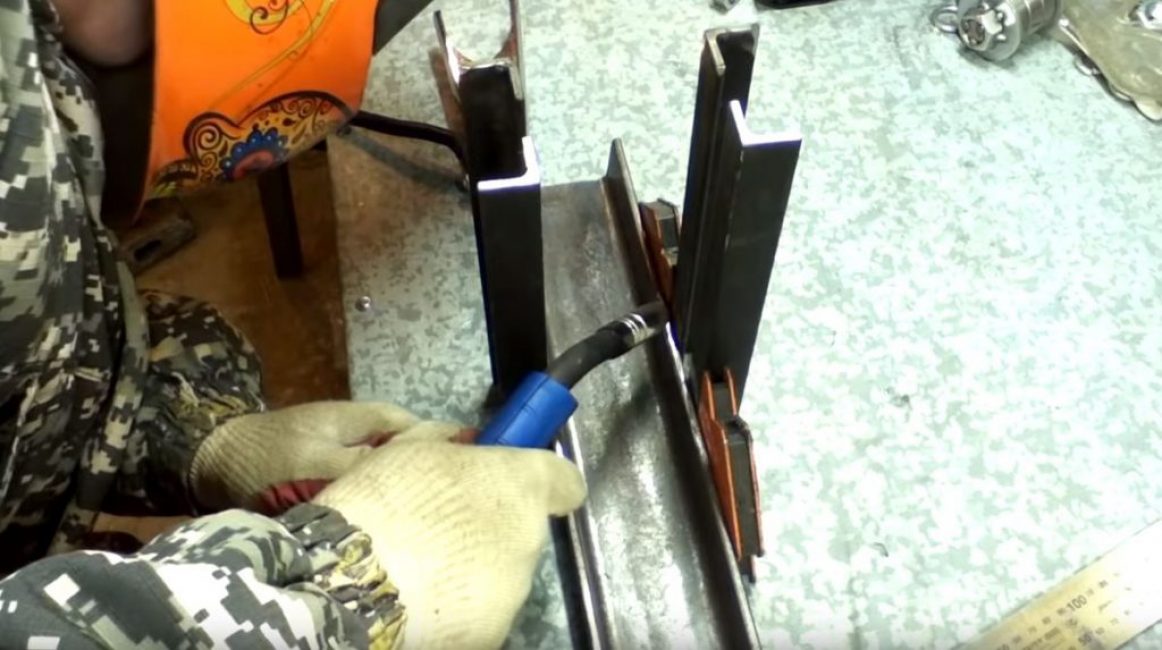
In the center of the third cut off stud we put on a piece of pipe with a diameter of 27 mm and a length of 40 mm. The cavity between the pipe and the stud is filled with nails. Weld the pipe to the stud.
We put on two bearings along the edges.
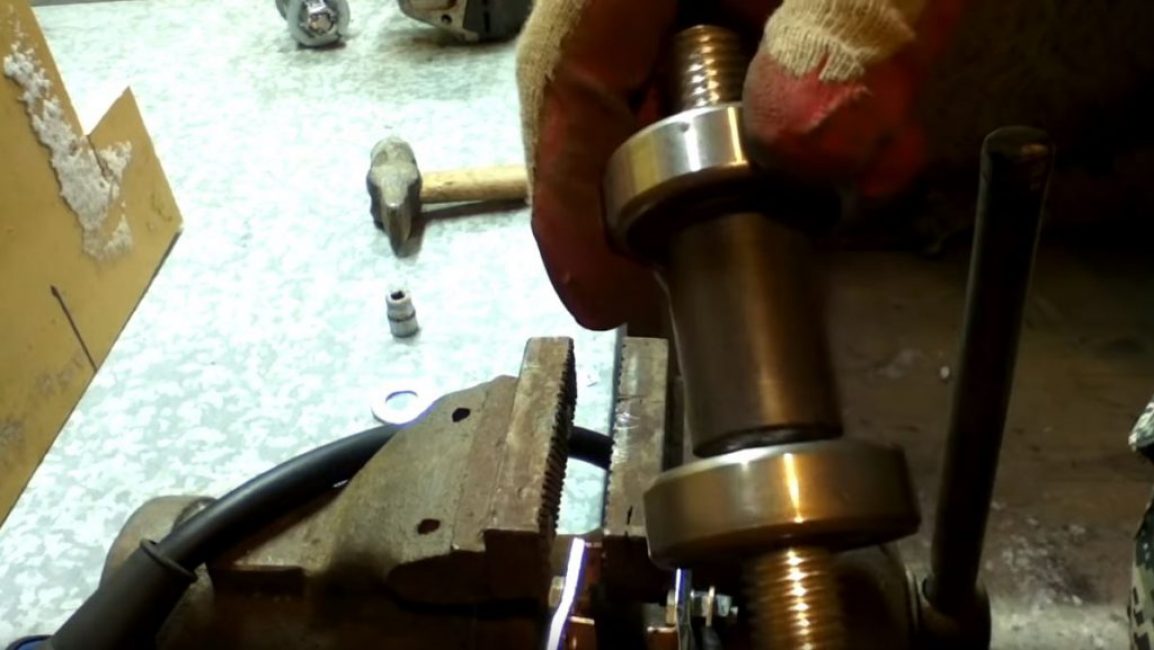
We cut off 2 pieces of 30 mm from the profile pipe 20x40 mm, cut a rectangle 80x50 mm in size from the plate.
We weld the cut parts with a shaft with bearings and get a movable carriage.
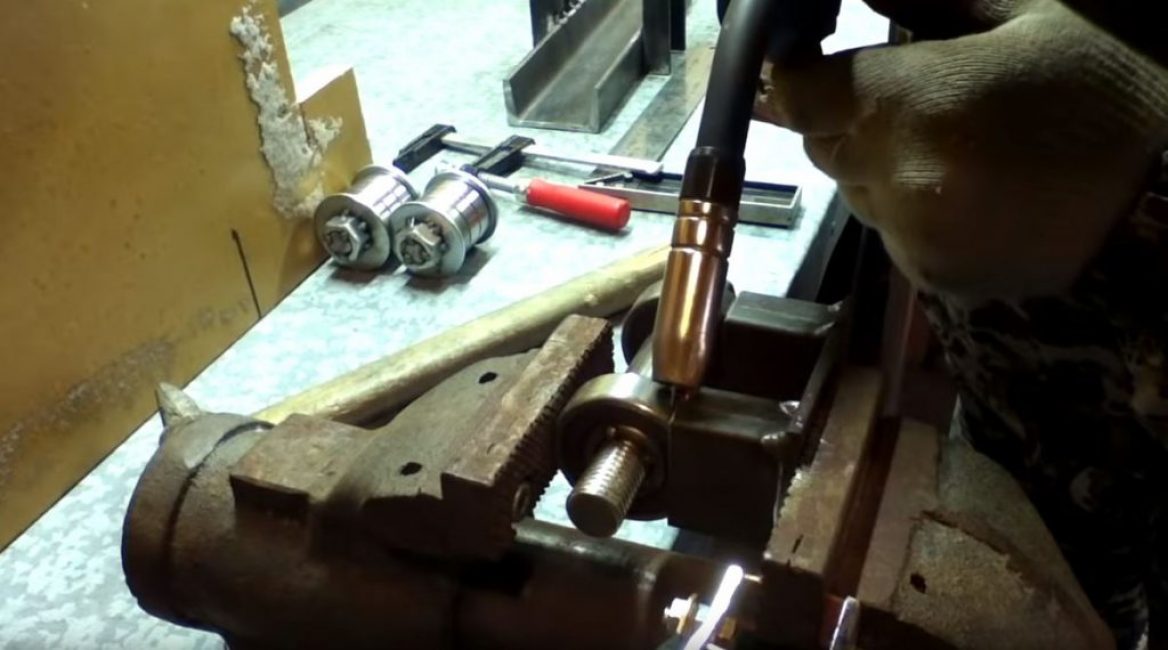
We drill a hole ø18 mm in the center of the plate.
We insert a stud into the drilled hole, screw nuts on it on both sides and weld them by electric welding.
We cut out a rectangle measuring 70x13 mm from a sheet of metal to stop the lifting mechanism. We also drill a hole ø18 mm in the center of it.
We thread the carriage with the roller into the guides, put the plate on top, screw the nut onto the stud and weld it to the plate by welding. The result is such a lifting and clamping mechanism.
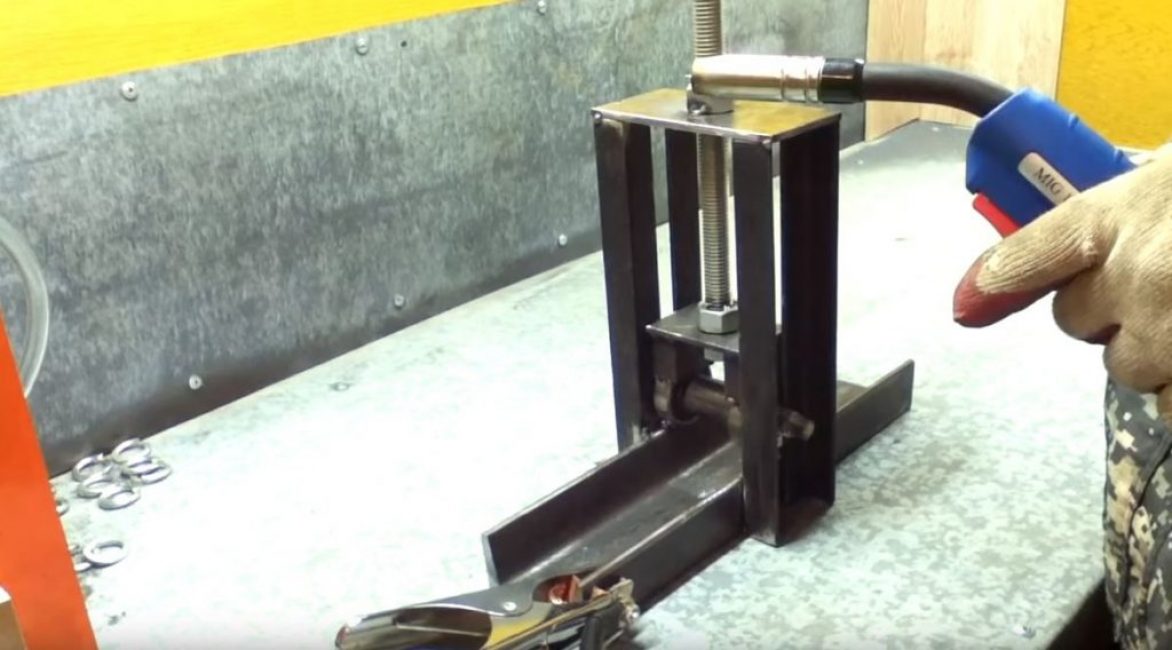
Step 4. The final stage
Along the edges of the profile, we weld the rollers made in step 2.
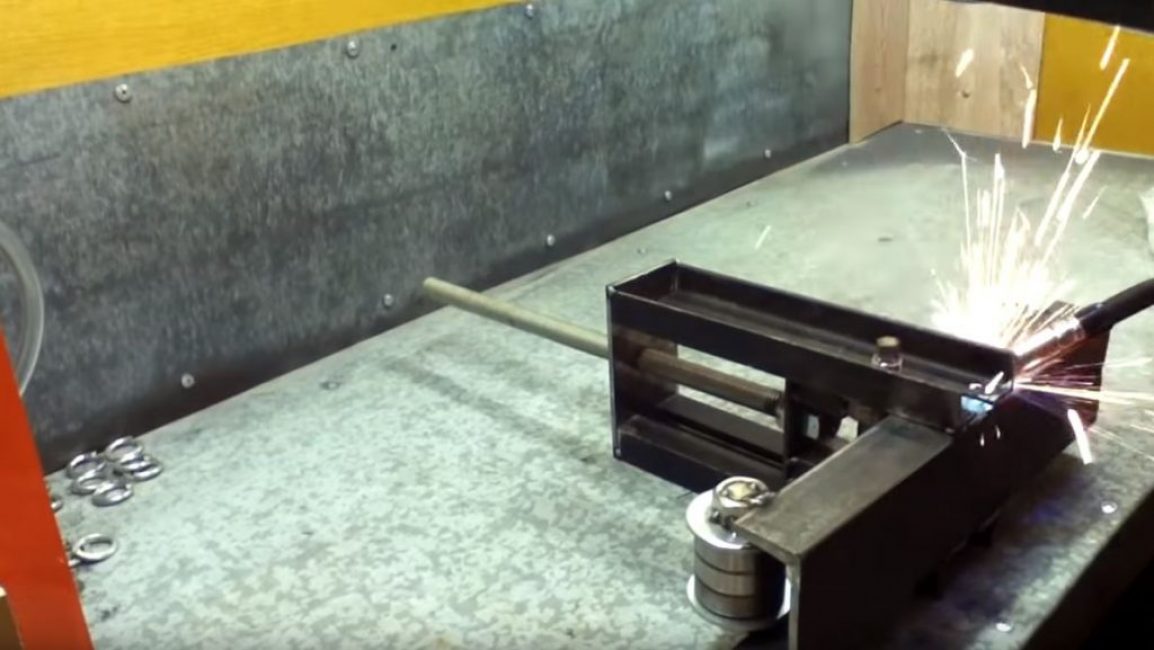
We cut out a handle for the lifting and clamping mechanism from a smaller profile pipe and weld it to the edge of the stud.
From the same pipe we cut out a lever for a mechanical drive 25 mm long. We drill a hole at one of the edges and insert a handle from any old tool into it. We weld the second end of the lever to the carriage pin.
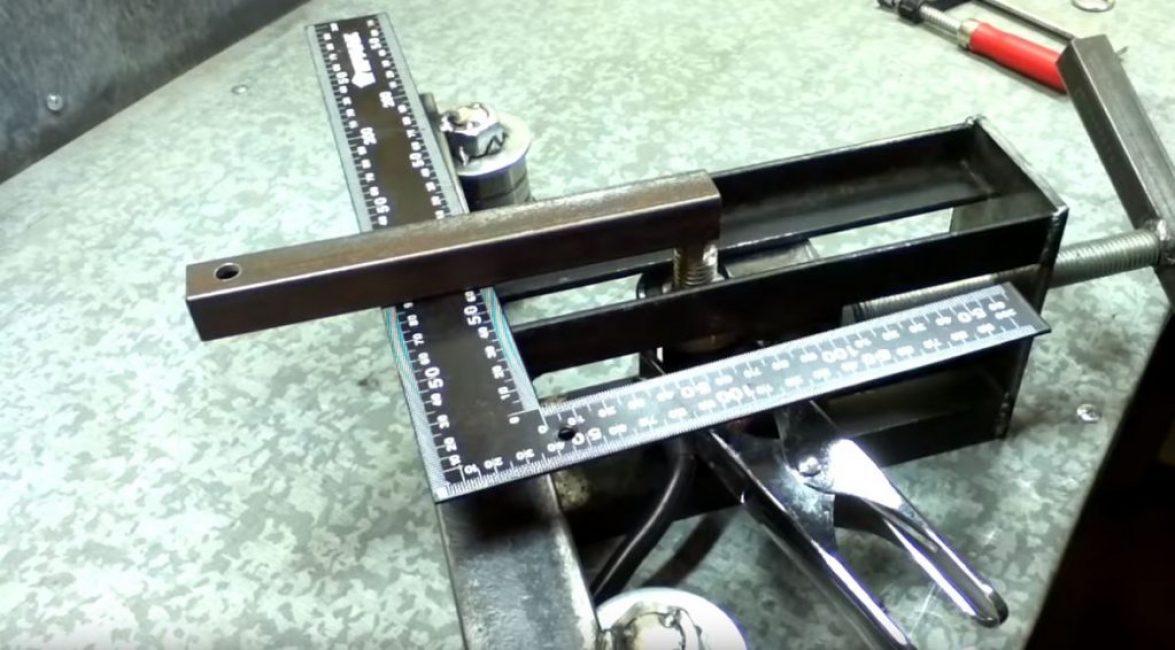
Tests fully confirmed the performance of our pipe bender.
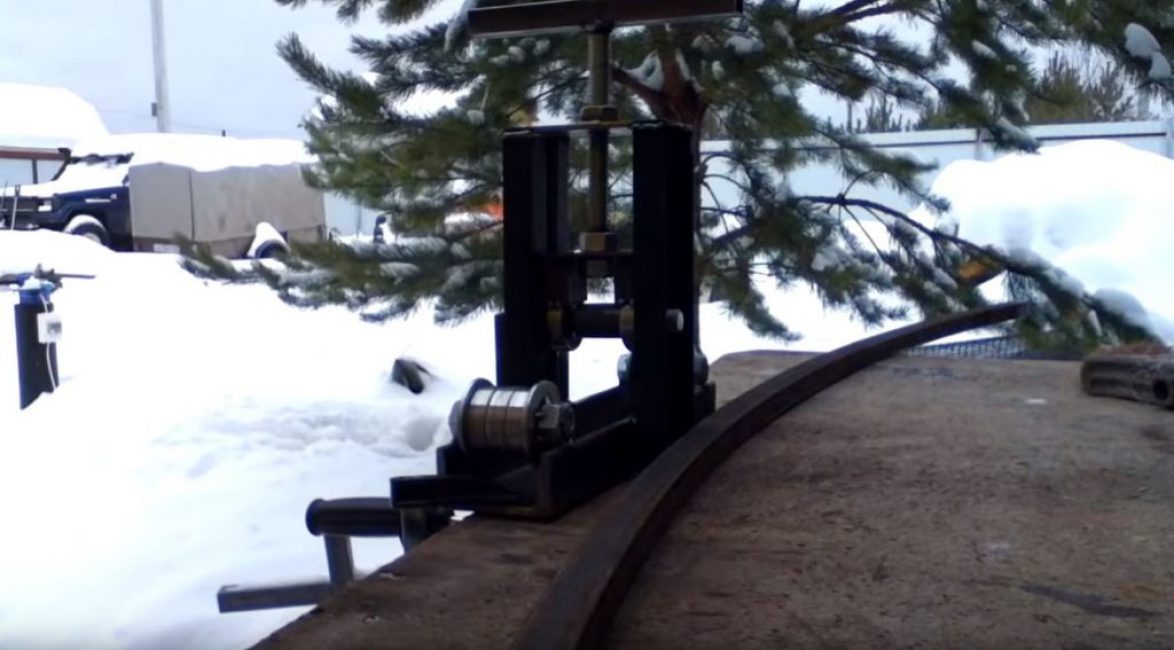
Video: Pipe bender without turning
Pipe bender without turning
How to make a pipe bender with your own hands? | Video