If you have ever been involved in the installation of plumbing, then you know that it is impossible to foresee everything. At some point, it turns out that there is a lack of a threaded coupling, purchased pipes need a reliable connection, etc. And it's good if a plumbing supermarket is nearby. Otherwise, our article may come to the rescue. In it, we will tell you how to cut threads on polypropylene pipes and couplings, how to achieve their reliable connection in various versions, which can withstand a pressure of 45 atmospheres.
Content:
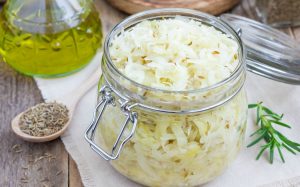
Materials for manufacturing
For threading and testing you will need:
- segments of polypropylene pipes;
- soldering iron for PVC pipes;
- die;
- metal coupling with external and internal thread
- plastic sleeve without thread;
- pipe cap;
- a pair of pipe wrenches;
- linen tow;
- sealant;
- high pressure test stand.
Method 1. We cut a thread on a propylene pipe using a cold mechanical method with an ordinary die
We put on the die and turn the pipe with a pipe wrench, driving it in the die to the desired distance. We do this carefully so as not to weaken the pipe by making dents on it.
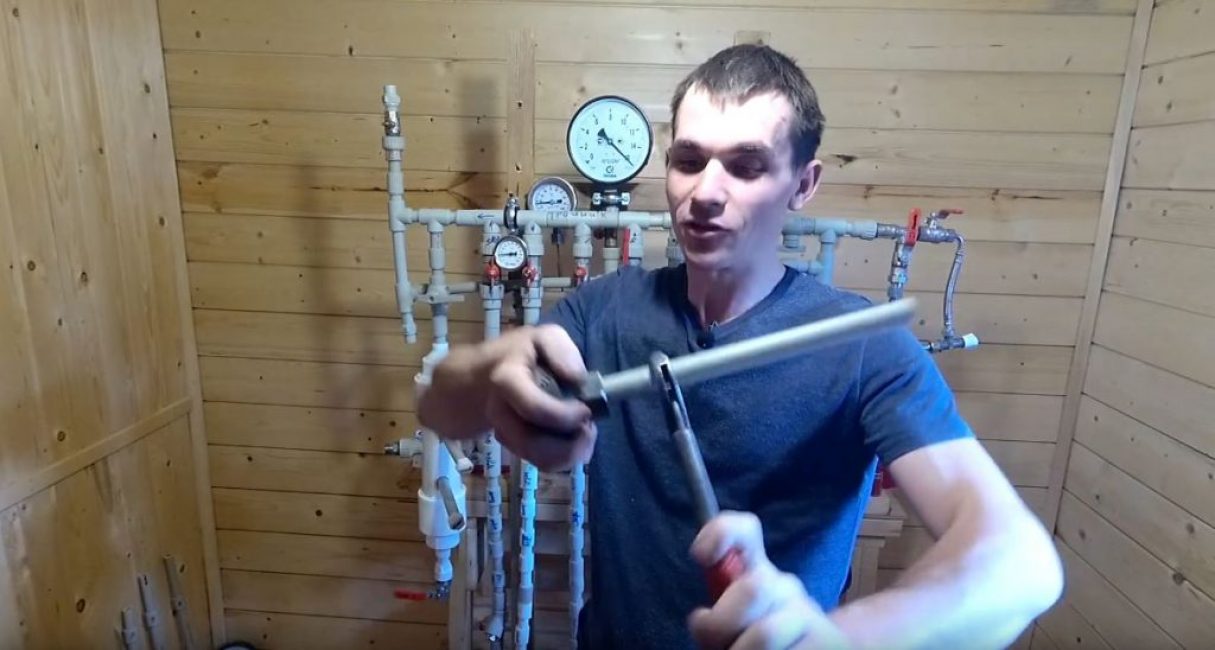
As a result, we get just such a thread: it looks unpresentable in appearance, but we will postpone the final conclusions until the test.
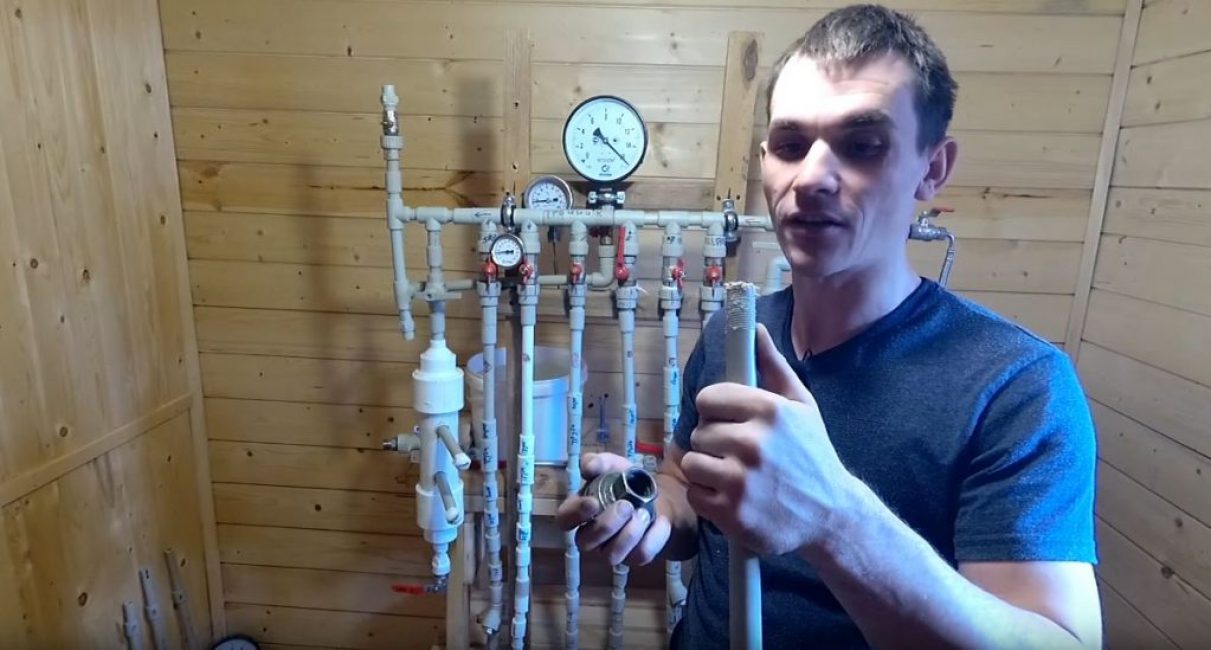
Method 2. We cut the thread using a welding machine for plastic pipes and a metal coupling
We heat the second end of the polypropylene pipe in the welding machine until it softens.
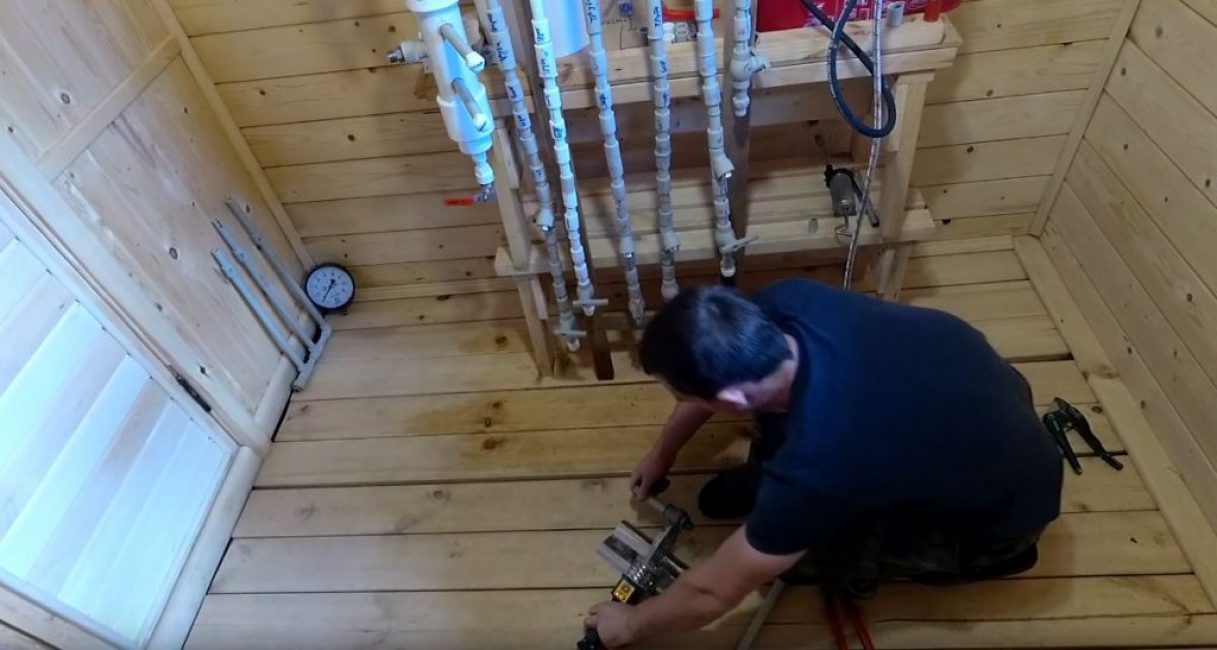
We screw it into the finished metal sleeve.
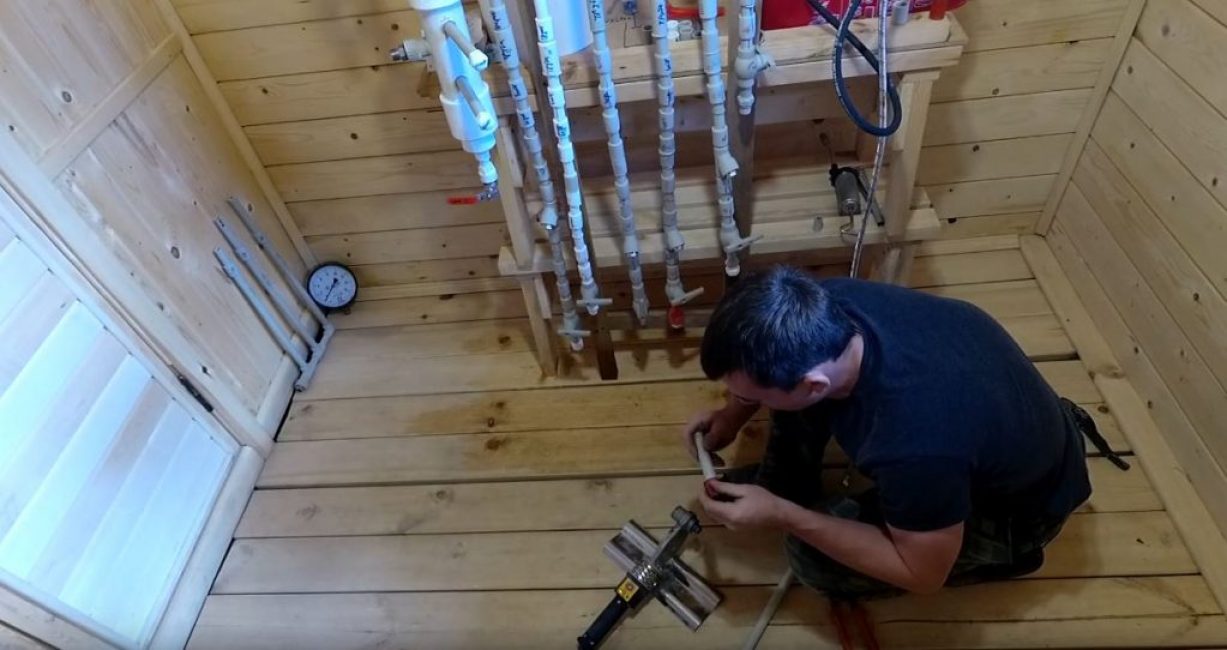
Let the compound cool down. The pipe can be easily unscrewed from the coupling.
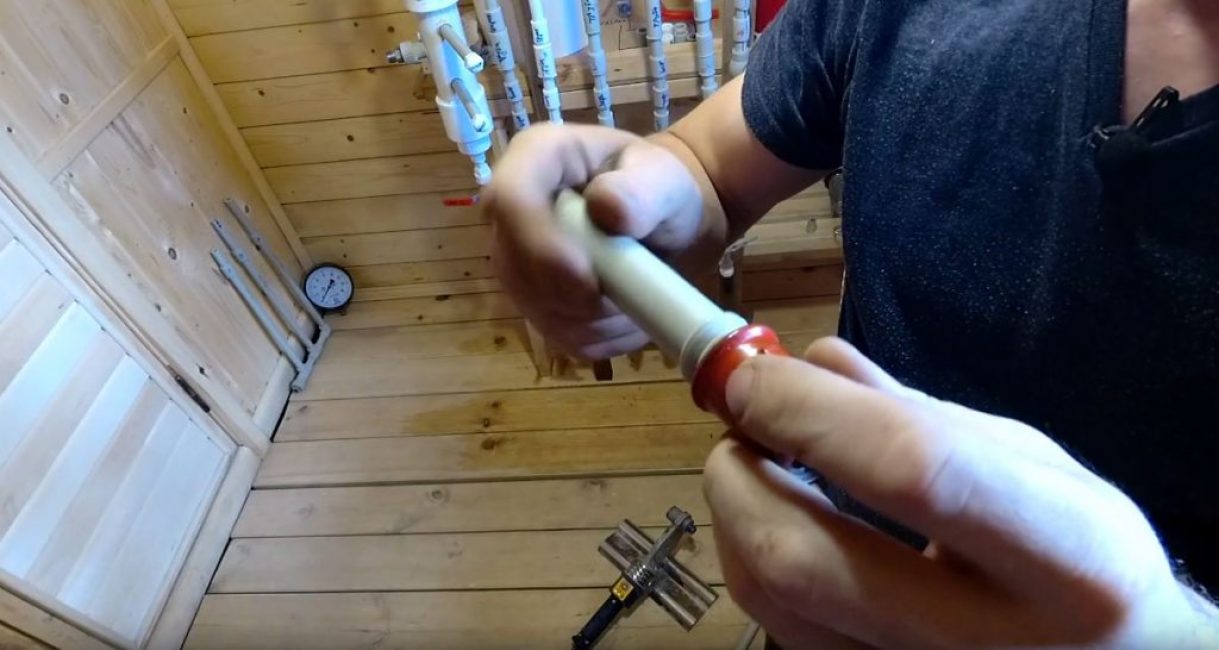
As a result, we get such a thread: at the beginning it was almost not cut, but at the end it has a pretty decent look.
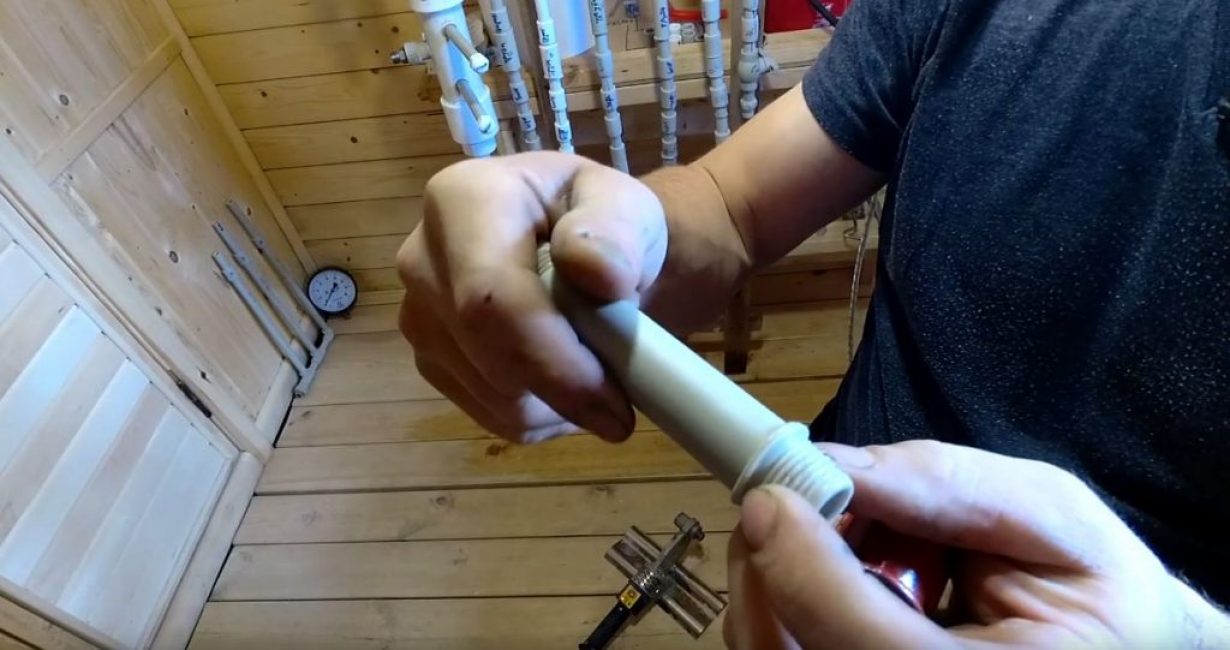
Source: https://youtu.be/o7wC7v5KAZ8
Method 3. We cut the internal thread on a plastic sleeve using a soldering iron and a metal sleeve
We heat the plastic sleeve on the welding machine.
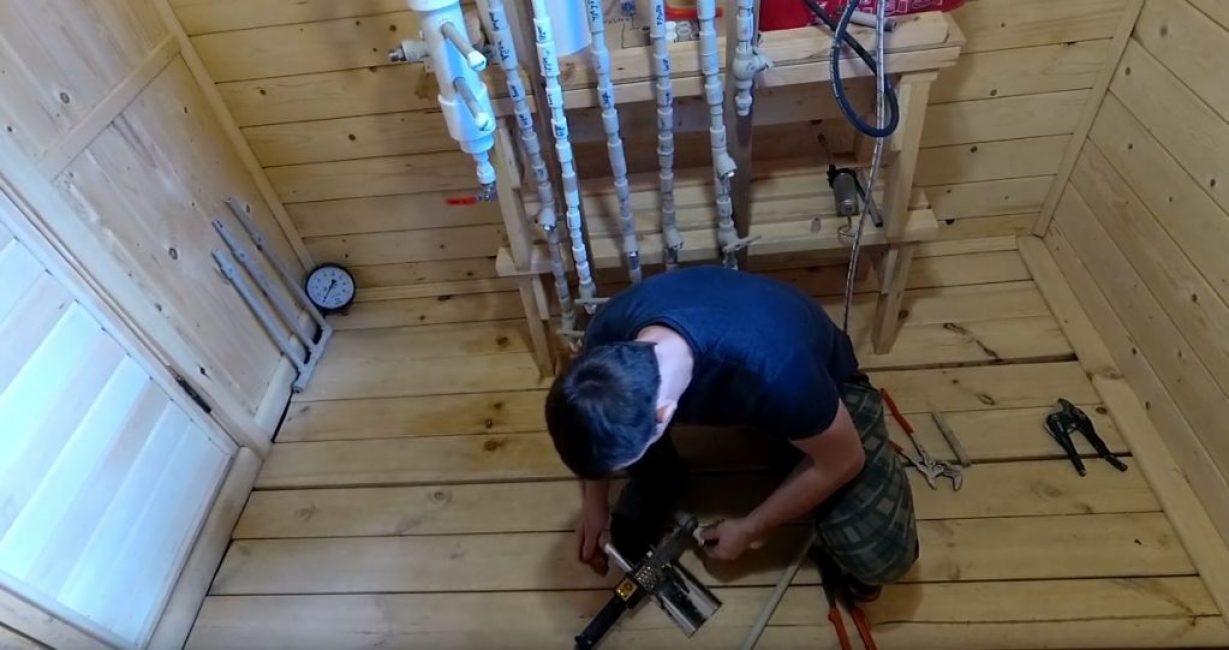
We screw the metal into it.
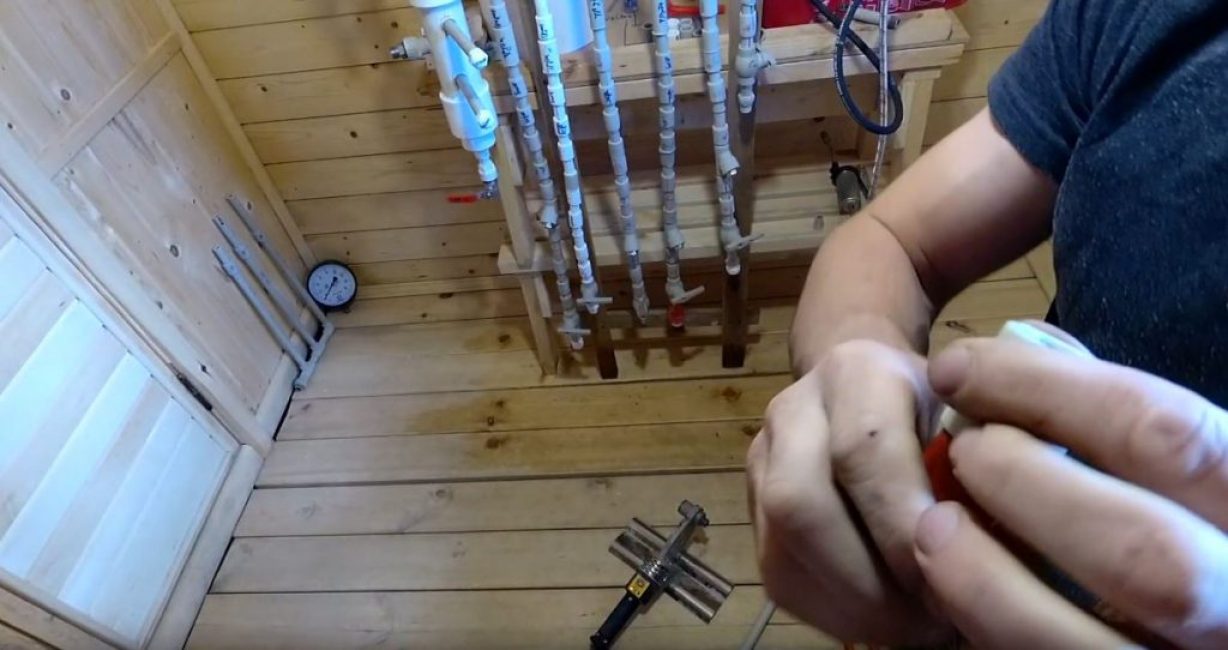
Let the plastic cool and unscrew the metal sleeve. The thread turned out almost like a factory clutch.
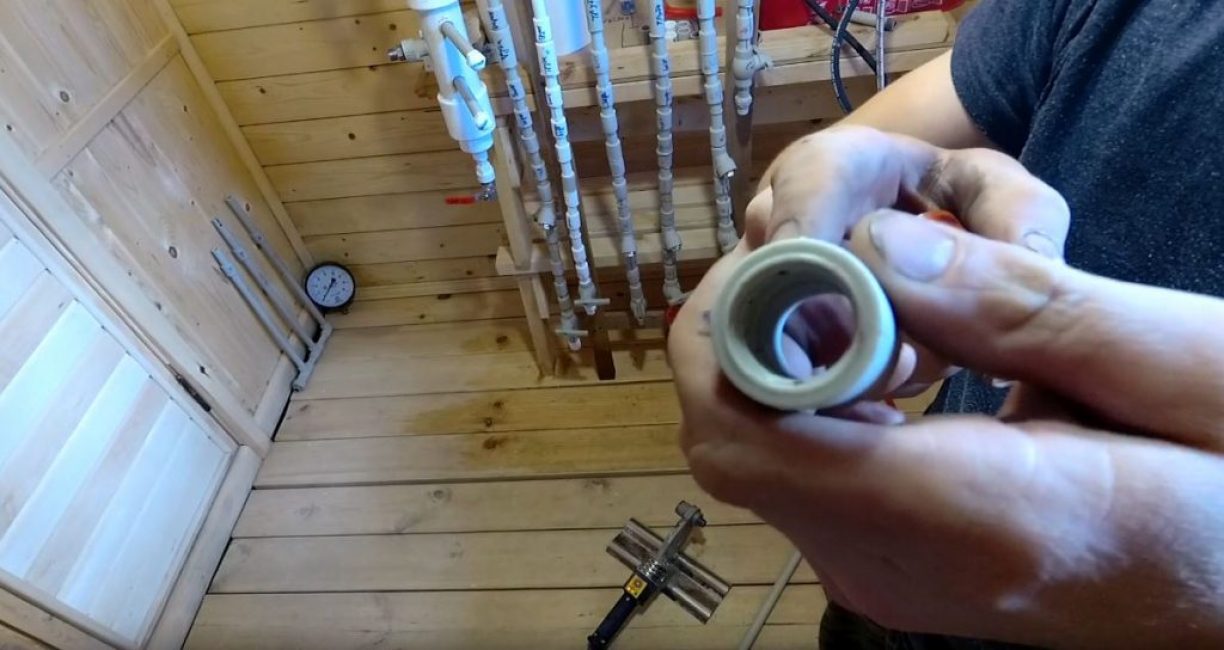
Do the same with the other side of the clutch.
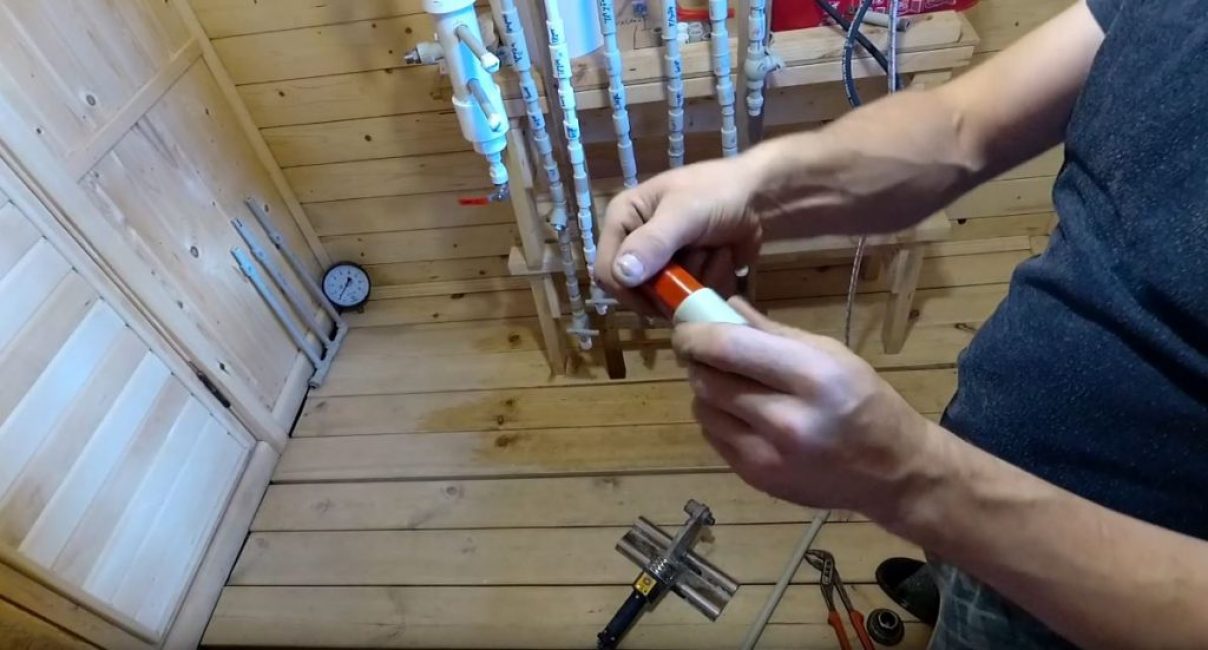
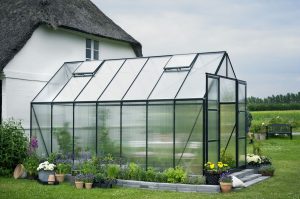
Assembling the design for testing
We connect all blanks to linen tow and sealant.
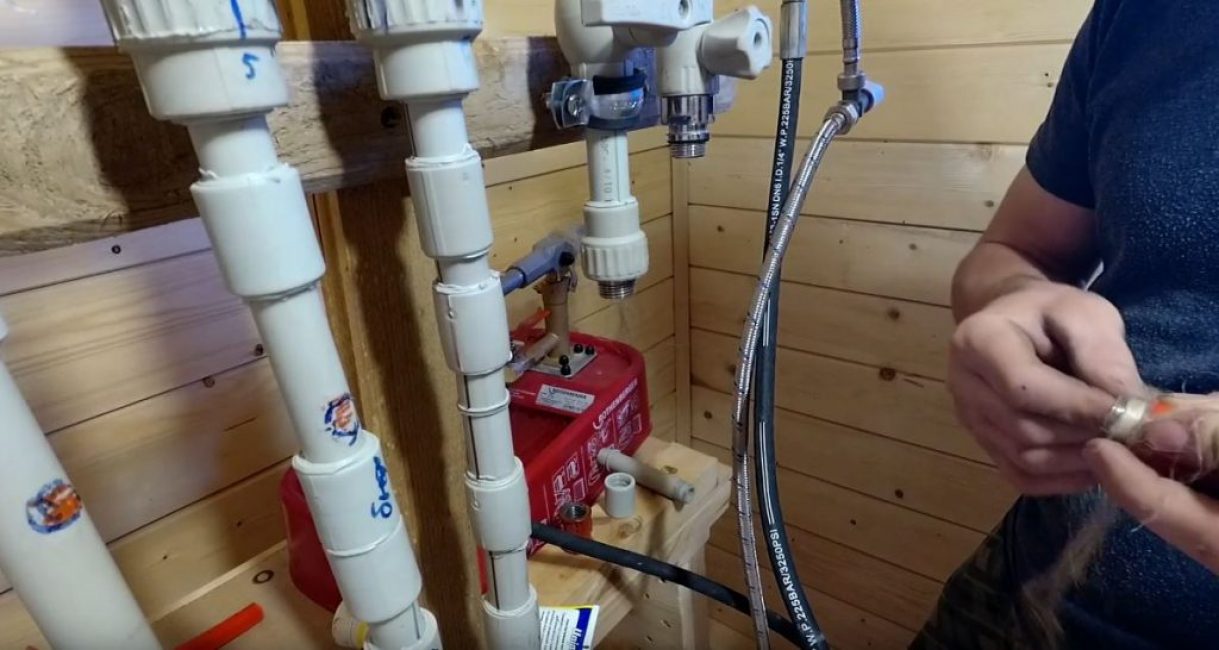
First, we screw the metal sleeve into the plastic one.
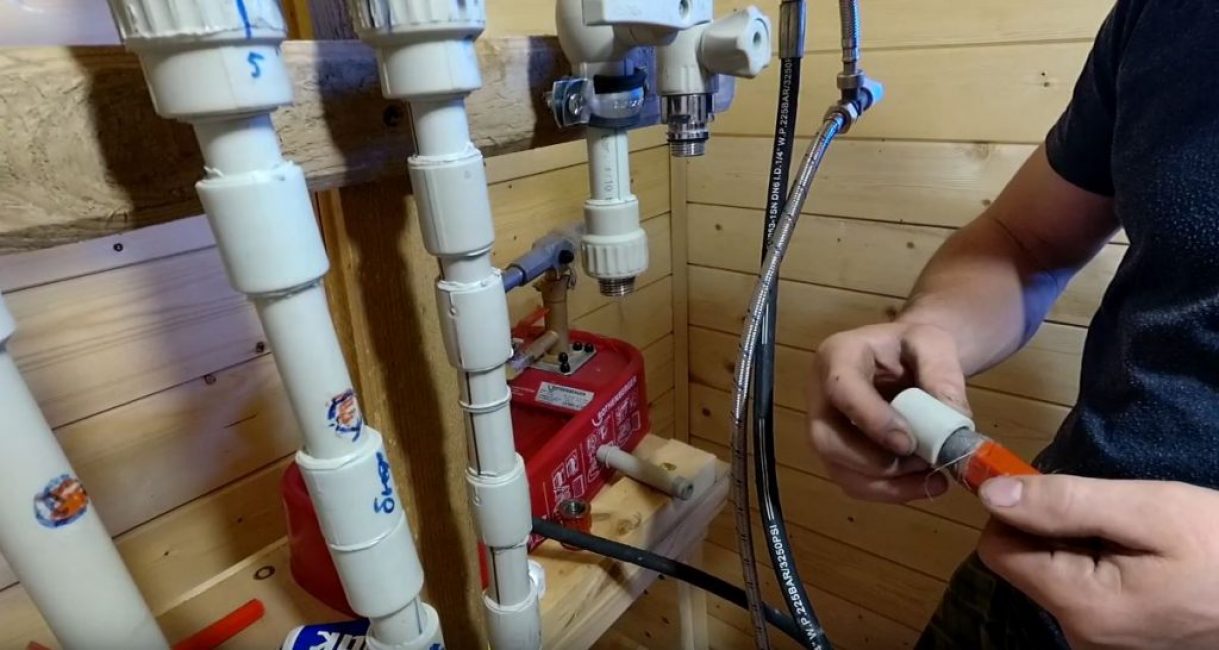
If necessary, the connections can be tightened with pipe wrenches.
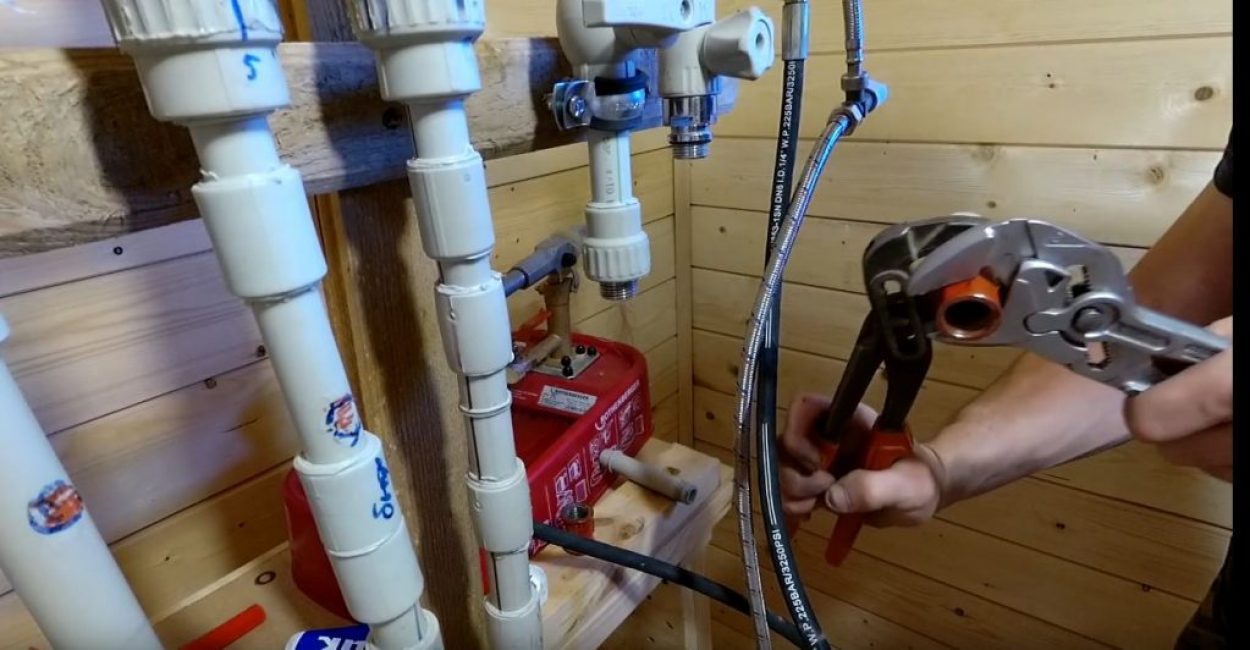
In the opposite direction of the metal coupling, we screw, also on tow and sealant, a plastic pipe cut in a cold way.
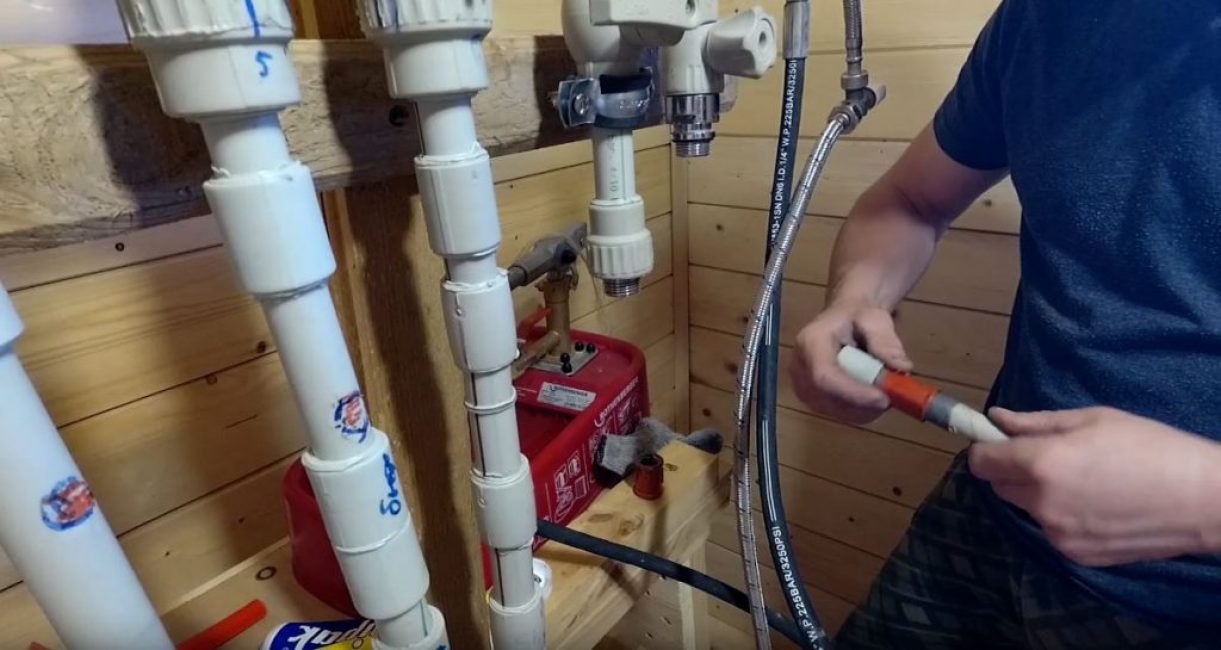
We wind another coupling on the second end of the plastic pipe.
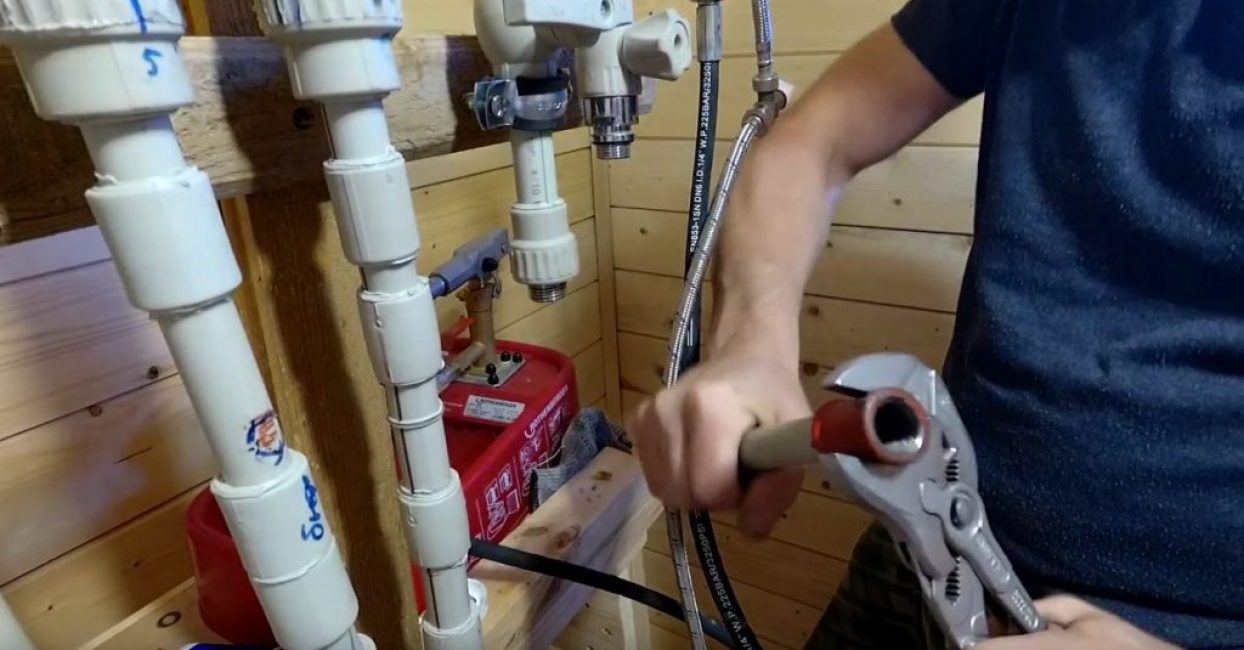
Testing
We connect the assembled structure to the test bench.
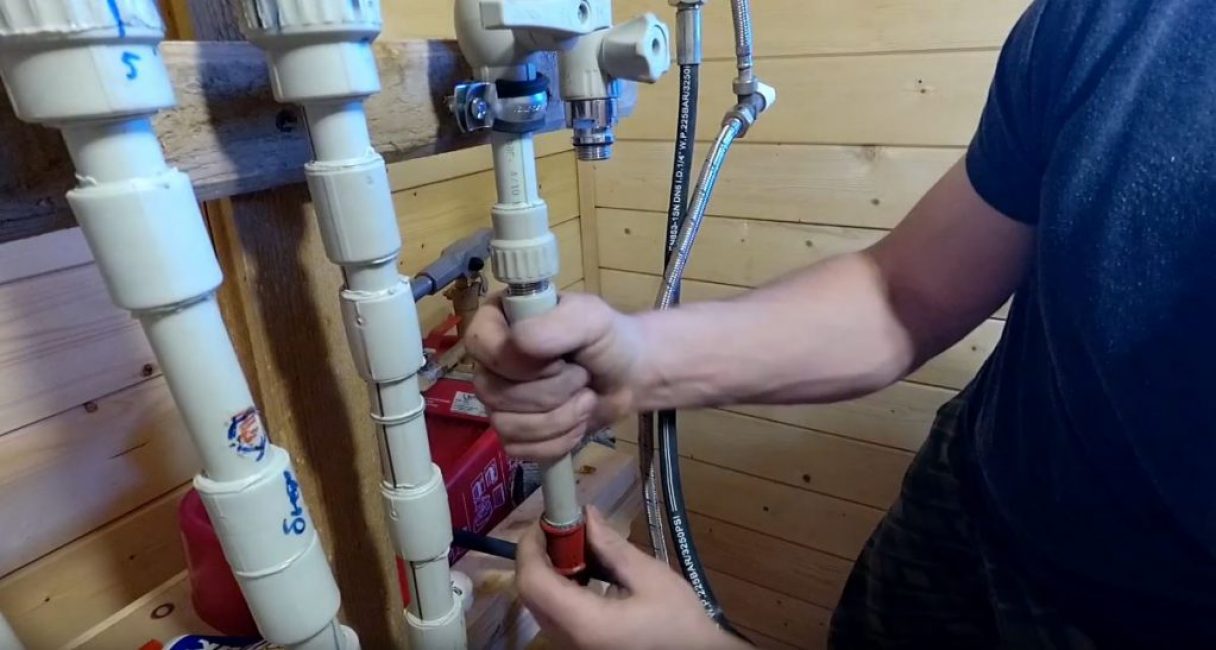
We twist the factory plug at the bottom.
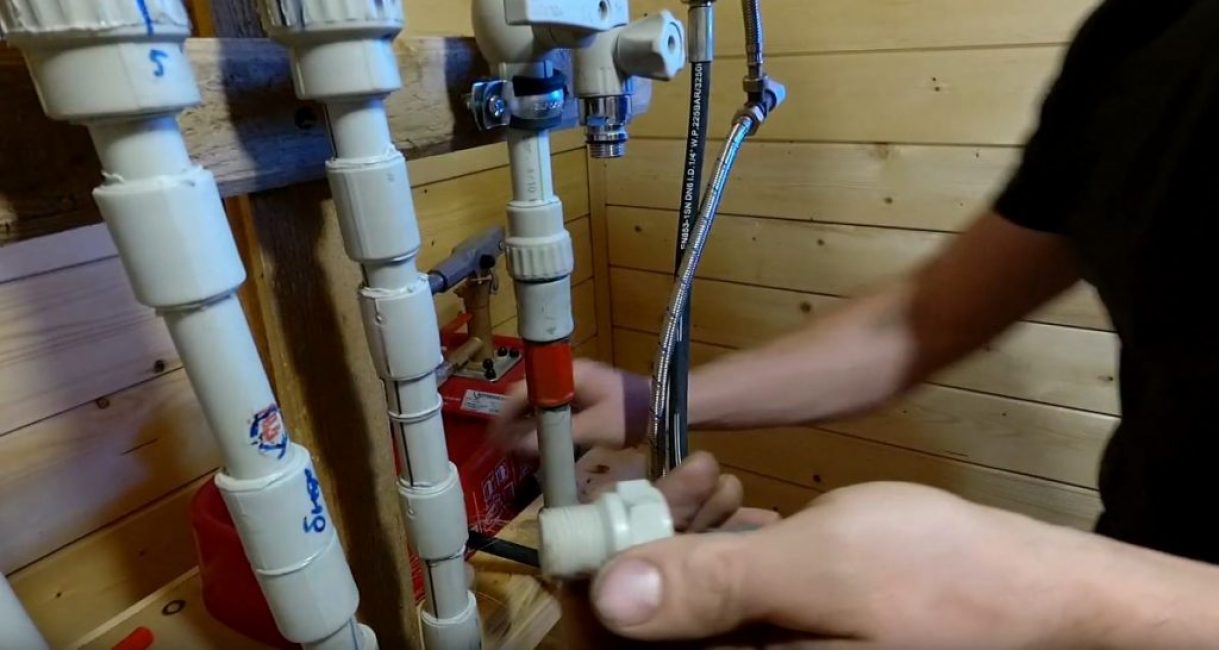
We apply pressure, gradually increasing it from 1 to 45 bar. Here we have reached a pressure of 20 bar.
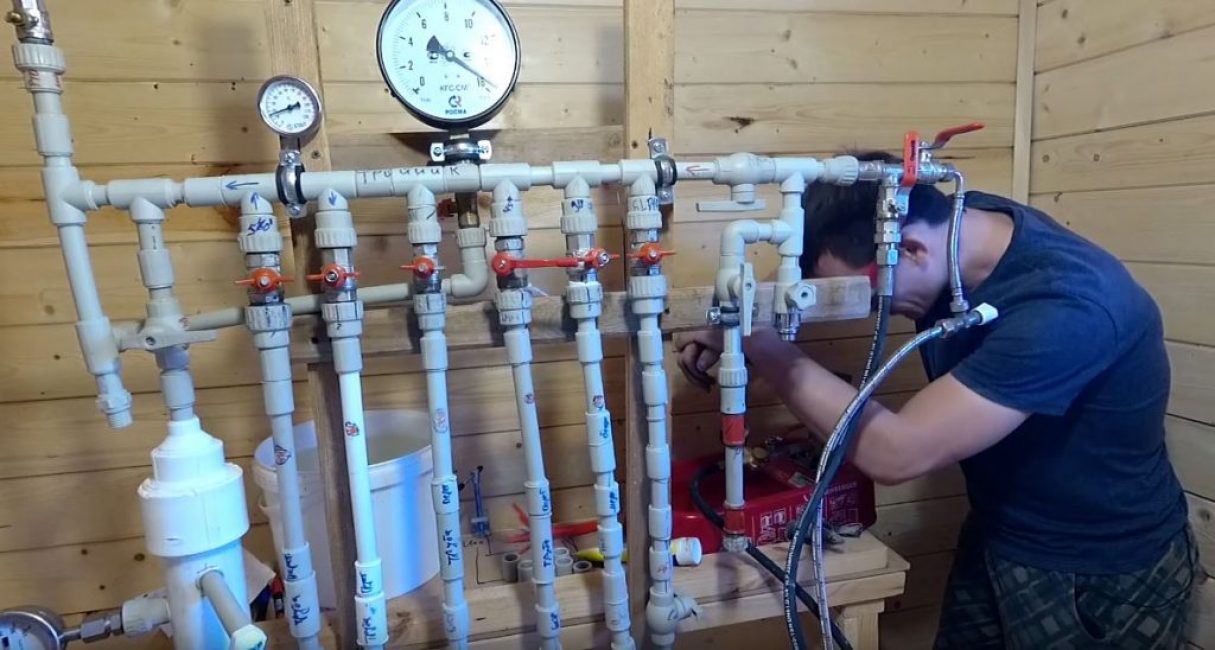
We increase the pressure to 45 atmospheres.
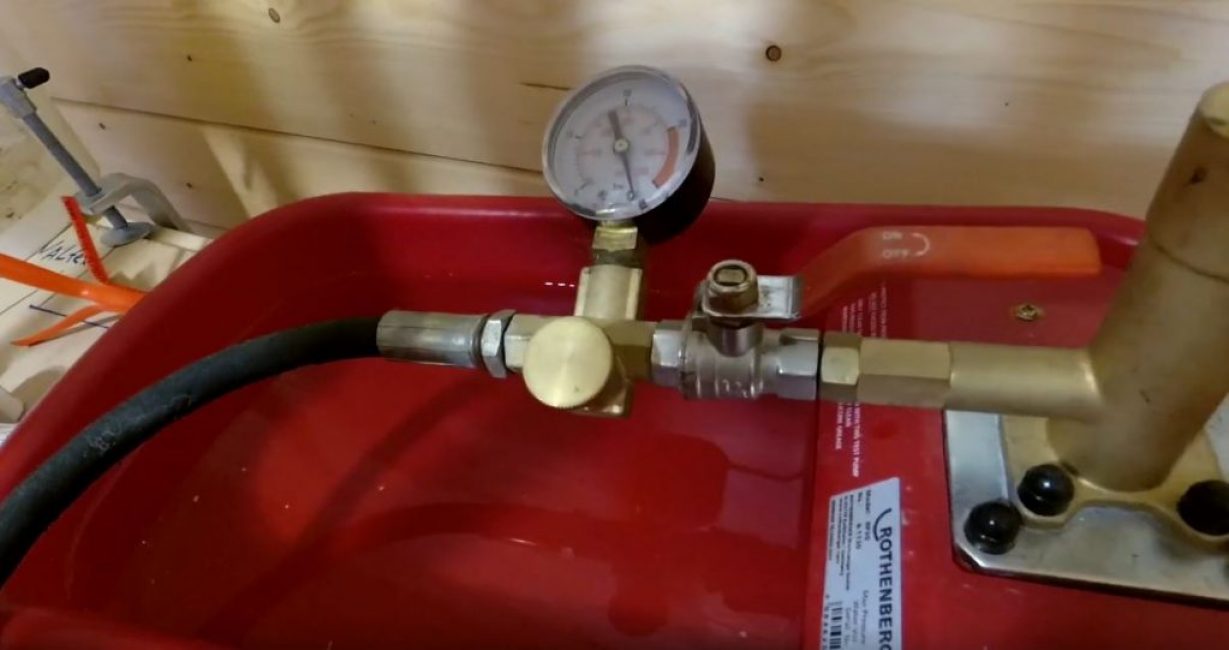
Video: How to make a homemade thread on a plastic pipe and coupling
How to make a homemade thread on a plastic pipe and coupling
How to cut a thread on a polypropylene pipe that can withstand a pressure of more than 40 atmospheres? | TOP 3 Ways