The most common cladding material building facades - plaster is not always the best solution. In winter, it is impossible to carry out “wet work”, a thick layer with a reinforced grating still exfoliates and cracks, without even providing minimal thermal insulation. Composite finishing materials - fiber cement panels - are deprived of all these shortcomings. How to use them correctly for exterior decoration will be considered in the material.
Content:
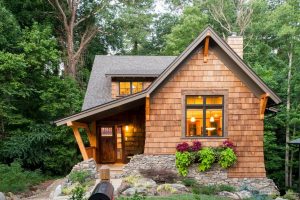
Material composition
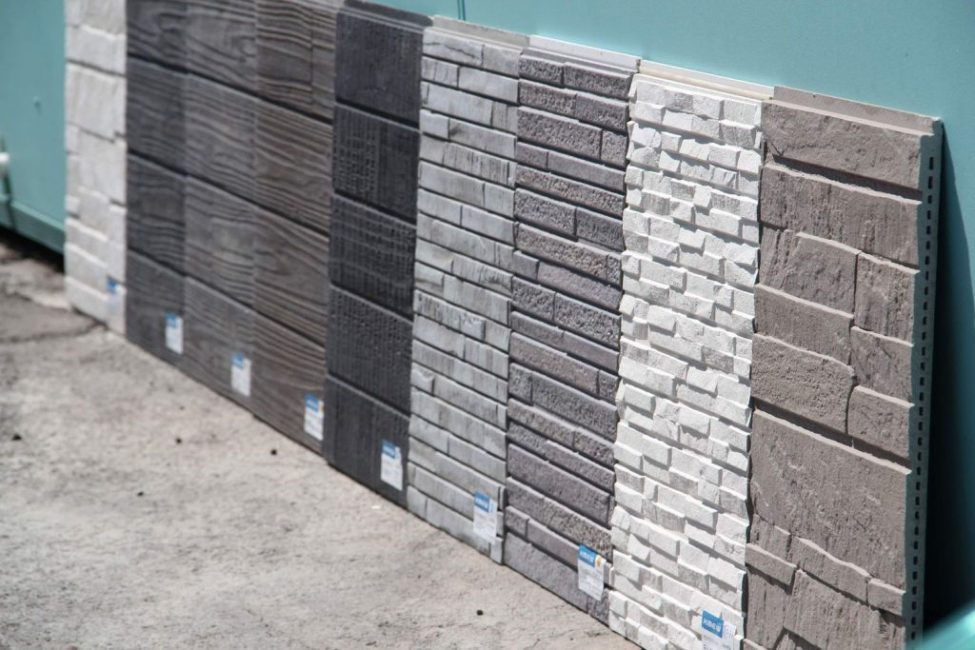
Fiber concrete slabs
Fiber cement panels are a material of artificial origin, which is used for exterior decoration of facades of buildings and structures. It consists of 9 parts of cement and 1 part of fiber - synthetic or cellulose fiber.
The finishing panel is a slab or board measuring from 1.2 to 3.6 m in length, from 19 to 150 cm in width and 0.1–3.5 cm thick. The sizes of facing plates from Russian, Japanese and European manufacturers are different. The weight of one element is about 10 kg.
Concrete gives the product strength, and randomly located fiber fibers - flexibility. The panel is based on a water-repellent primer that protects the building material from moisture absorption, and the surface is supplemented with a weather-resistant coating that also performs a decorative function.
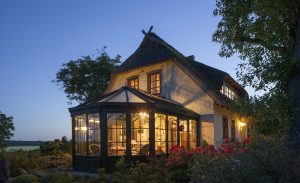
Technological process of production
Fiber cement panels are produced industrially by pressing or using an autoclave. In order to obtain a uniform structure and density of the siding, the raw materials (cement, cellulose and sand) are mixed, molded and rolled out.
Then the resulting layer of raw fiber cement on the conveyor belt is cut into separate panels of specified parameters. The slab blanks are stacked.
The stacks are pressed under a pressure of 600 N/cm2 (approximately 59 atmospheres) at a temperature not lower than 170 degrees. In the process of pressing, excess moisture is removed from the material, a uniform density is created and strength is enhanced.
The next production step is accelerated process of solidification of panels in the chamber for thermal and moisture treatment. It is during this step that the material acquires hygroscopic properties.
Then the fiber cement is sanded and painted with a smooth or textured paint. As an additional protection against external negative impact, the manufacturer may cover siding varnish, including anti-vandal.
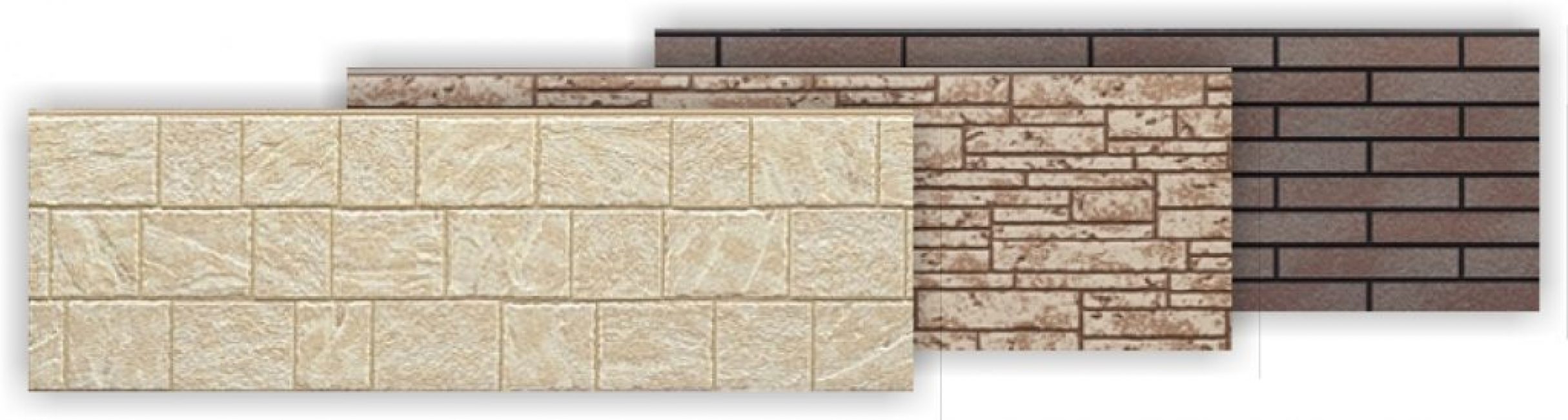
Sample textures and colors
Depending on the applied pattern, the panels can imitate:
- masonry
- tree
- brick
- stone chips
- plaster
- monochromatic coloring
Decorative texture of composite cladding - imitation of other building materials - created by using patterns during pressing.
Finished slabs are:
- laminated with vinyl coating or with a textured surface
- with regular and improved wet resistance
- small, large, in the form of siding panels
- conventional and with ledges for kleimers
- with normal and increased fire resistance (limit - 120 minutes)
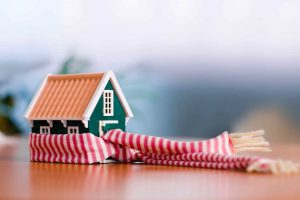
Advantages and disadvantages of fiber cement
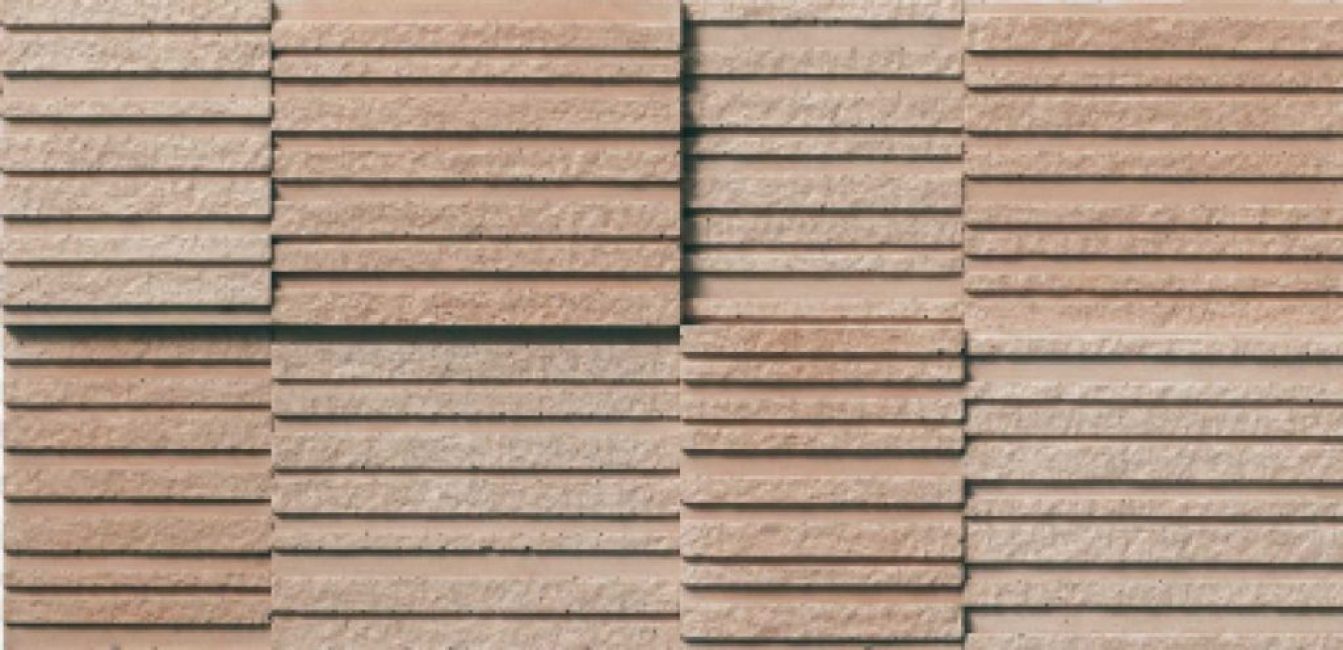
Fiber cement panels
Cement and fiber panels were created as a replacement for plaster, superior to this material in terms of performance for outdoor decoration. Advantages and disadvantages of fiber cement over other types of cladding:
- Durability. The material can last about 50 years without changing its physical and chemical properties
- impact resistance. Cellulose fibers give a reinforcing effect
- Flexibility. Plates can be bent so as to repeat the curves of the facade as much as possible
- Minimum load on supporting structures. The panels are quite light, which makes them a convenient material for installation and transportation.
- fire resistance. Siding from fiber, in addition to being decorative, it also performs a protective function, protecting the building from fire
- High vapor permeability and the ability to quickly absorb and evaporate moisture due to water repellents in the composition
- UV resistance. Fiber cement panels do not fade and do not lose their original appearance
- Safety. The material is considered environmentally friendly because it does not contain components potentially hazardous to humans.
- Resistant to low temperatures and sudden changes in weather
- Versatility and aesthetically pleasing exterior
- Noise canceling and thermal insulation properties
- Convenience and quick installation, minimal waste
- susceptibility to linear deformation of 2%.
Application
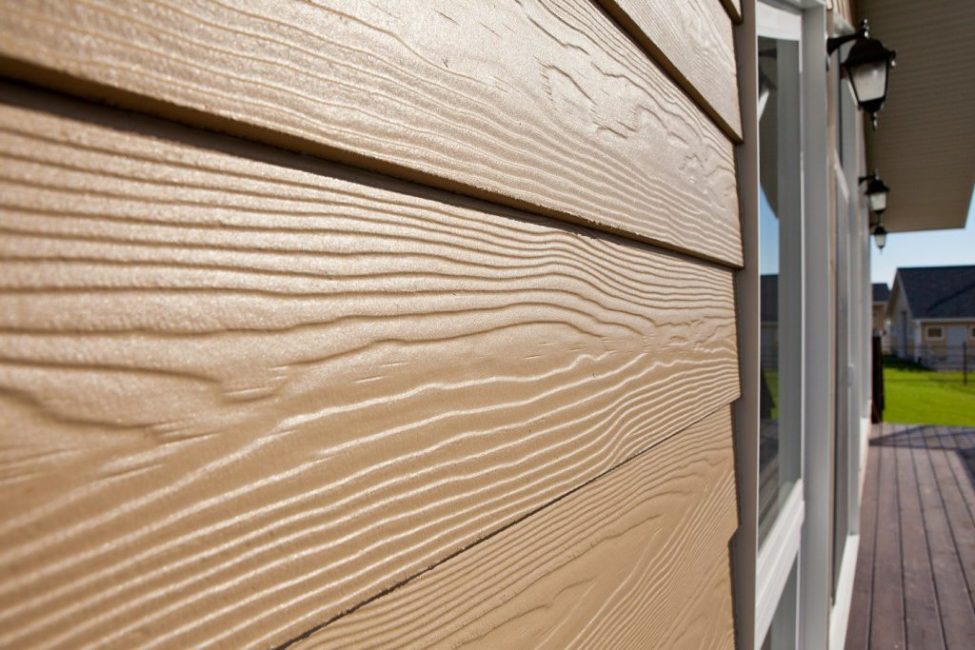
Composite finish
Fiber cement slabs are used for exterior finishes:
The material is used for insulation and lining of medical institutions, social facilities, in rooms with high humidity and fire hazard. The operational characteristics of siding determined its popularity for interior wall decoration of residential premises and decoration of fireplaces (due to refractory properties).
Fiber cement and fiber concrete slabs are different names for the same finishing material.
Smooth fiber cement boards are mounted with an overlap and imitate a profiled non-grooved board. Siding with special grooves, which is fastened end-to-end, is outwardly indistinguishable from a thin sheathing board - lining.
Fiber cement today is underestimated and rarely used. The low popularity of the material is associated with insufficient awareness of consumers about the properties of the composite.
Compared to plaster, it wins in most parameters:
- it can be mounted on any surface
- the risk of cracking is minimal
- the cladding process is simplified and does not require special skills
Trimming, drilling and storage of slabs
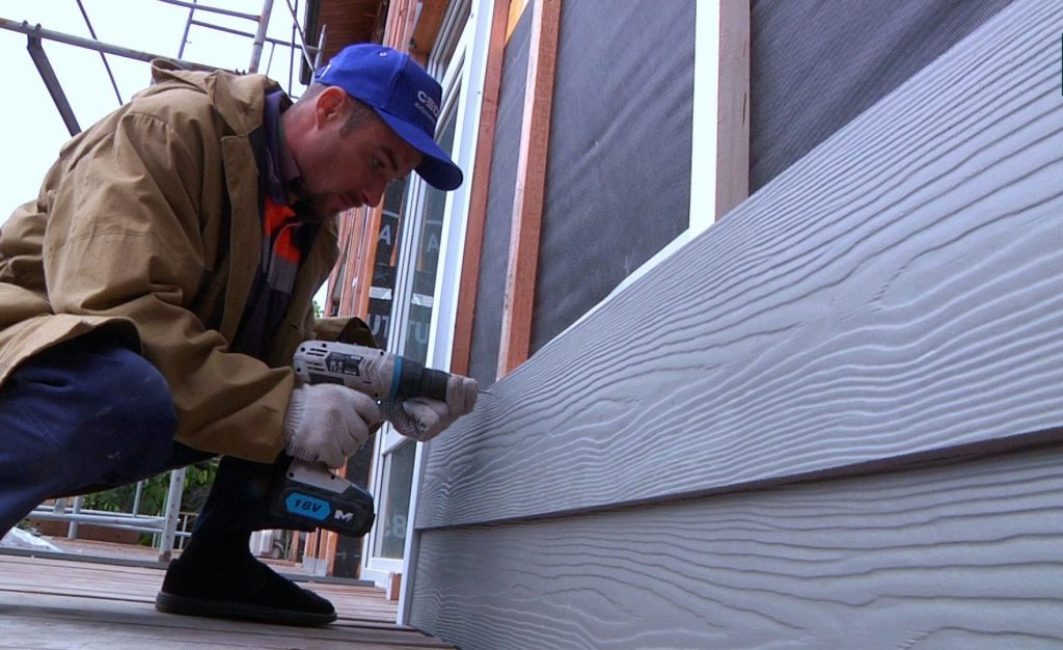
Drilling of fiber-reinforced concrete slabs
In the case of independent finishing work, you need to know the rules for handling fiber cement: its trimming, drilling and subsequent storage.
In order to cut a facade element of the required dimensions from a solid slab, you need:
- Place the panel face down on a soft pad to avoid scratches
- Mark cutting lines
- Cut out the details with a circular saw, observing safety rules. The tool at the lowest point must pass 0.5 cm lower than the fiber cement slab
- If necessary, grind the cut points and wipe off the dust with a dry cloth.
When drilling it is recommended:
- pre-marking
- drill one plate at a time
- use a drill with an appropriate sharpening angle
- make indents from the edges of the panel
Optimal storage conditions for fiber cement boards:
- horizontal
- on a flat surface, with material underneath
- it is not recommended to put on the ends
- put wooden blocks under the stacks
Painting fiber cement panels
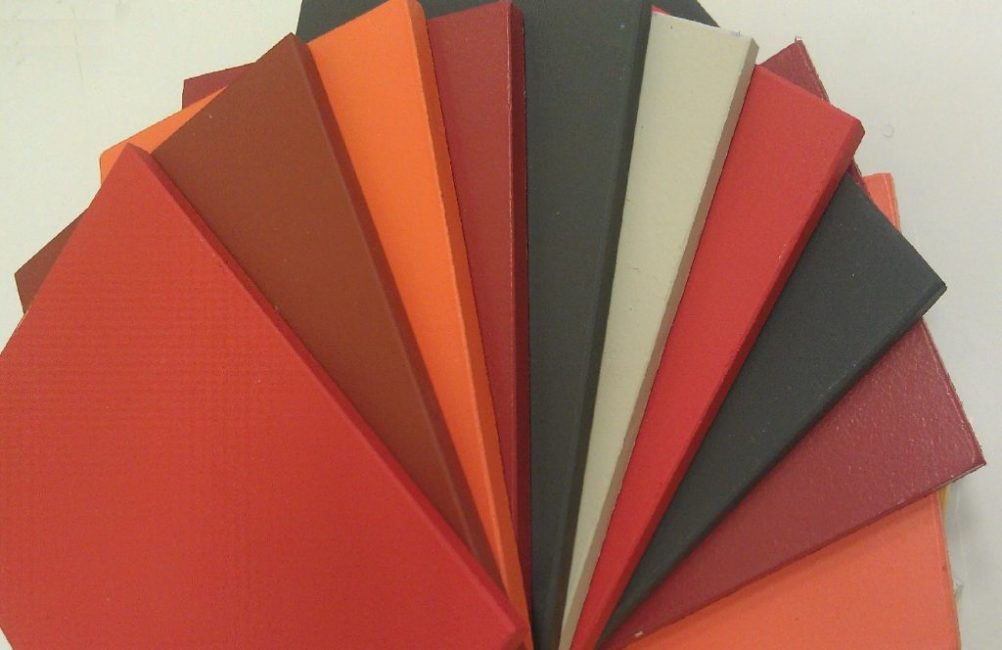
Painted composite boards
If unpainted plates are purchased, then with self-painting it is advised:
- Do not repair cracks and scratches with putty or other materials other than acrylic paint.
- Reject plates with defects on the front side - they cannot be eliminated on their own
- Dry the board before painting.
- Clean prepared sanded panels with compressed air
First, the fiber plates are treated with a roller with a concrete surface fixative diluted according to the instructions - fluate. The substance dries no longer than half an hour. Then the building material is left in a room with a temperature of +20 degrees and a humidity of 50% for a day.
The next layer is impregnation, which dries for a day at a temperature of 20 degrees. 2 hours before the start of staining, it is recommended to tint the paint. Apply it with an airbrush or air gun in one layer with a wet film thickness of about 100 microns.
Drying ideally takes place in a dryer with a constant temperature of 50 degrees and 50% humidity. Each layer dries for at least 3 hours. Complete polymerization of the paint occurs after 5 days. After the final coat of paint, the panels are sanded.
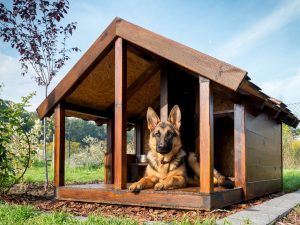
Self-assembly
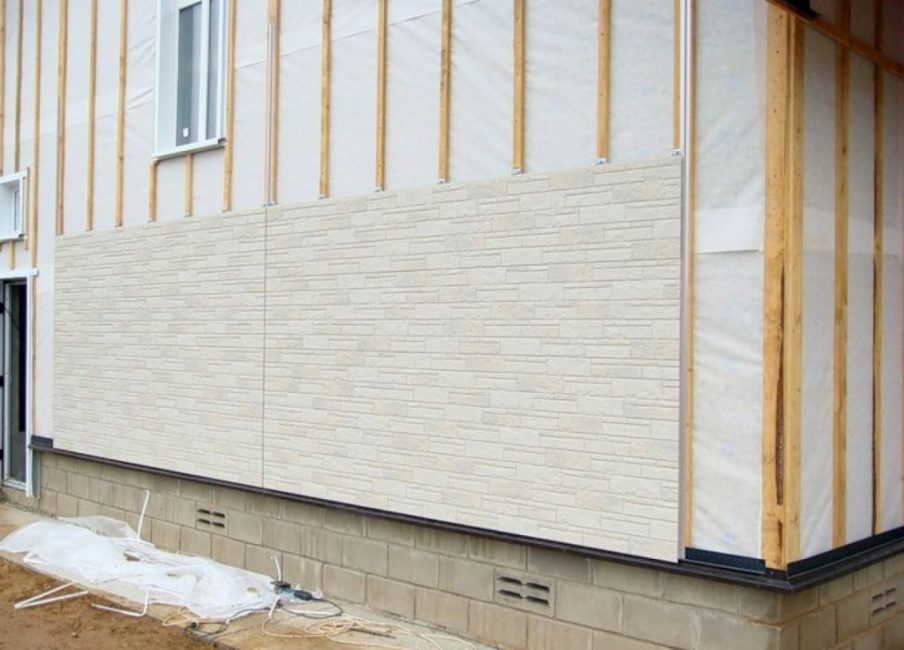
Ventilation facade installation
Facing of buildings with decorative panels is carried out by a hinged method on a metal profile frame. Mounting is carried out on both horizontal and vertical rails.
Before installing the slab on the facade, the walls of the building or structure must be prepared: cleaned of dirt, paint residues, finishes, concrete mortar, rust. With the help of beacons and a building level, the vertical surface is leveled if necessary. When setting the plane of the facade, plumb lines are used.
For self-fastening plates, you will need the following tools:
- screwdriver
- perforator
- knife
- roulette
- hammer
- scissors
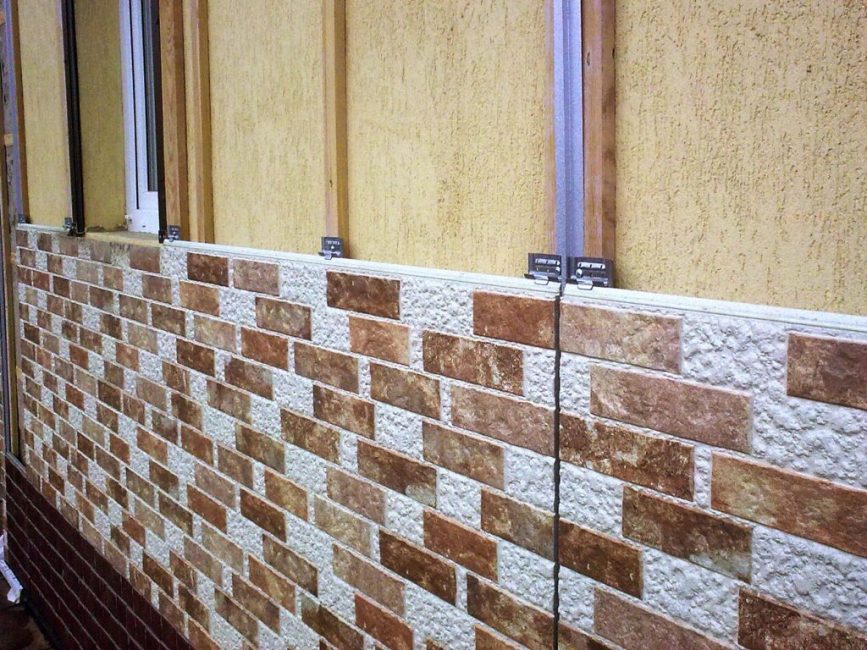
fiber cement siding
Installation takes place in accordance with the instructions:
- Places for mounting brackets are marked on the wall at intervals of 1 m in length and 60 cm in width
- Drill holes for anchors
- With the help of anchor bolts, the assembled brackets are fixed to the wall. The length of their working part is regulated by plumb lines, taking into account the gap for insulation
- A paronite gasket is installed between the wall and the bracket, which protects the metal from corrosion.
- A layer of mineral wool with holes for brackets in the right places is attached to the wall using dowels. Insulation plates are mounted in a checkerboard pattern to improve thermal insulation properties
- Vertical frame profiles made of aluminum or steel are installed, which are connected with rivets and tires
- Mounting holes are drilled in the plates, they are leveled and attached to the profiles with self-tapping screws.
- Additional fasteners are installed using fitted skids
- A gap is left between the fiber cement panels, the slopes are sealed with metal parts, and the joints are treated with sealant
- Fastening goes from top to bottom using the lock-to-lock method
The panels, as a rule, are equipped with ventilation slots for free air circulation between them and the insulation. When installing the ventilation facade, 2 crates are made: along the wall of the house horizontally and vertically along the insulation with a vapor barrier membrane. At the same time, cornices and shutters are mounted last.
![[Instructions] How to make beautiful and unusual wall shelves with your own hands: for flowers, books, TV, kitchen or garage (100+ Photo Ideas & Videos) + Reviews](https://iherb.bedbugus.biz/wp-content/uploads/2018/05/19-6-300x213.jpg)
Installation nuances
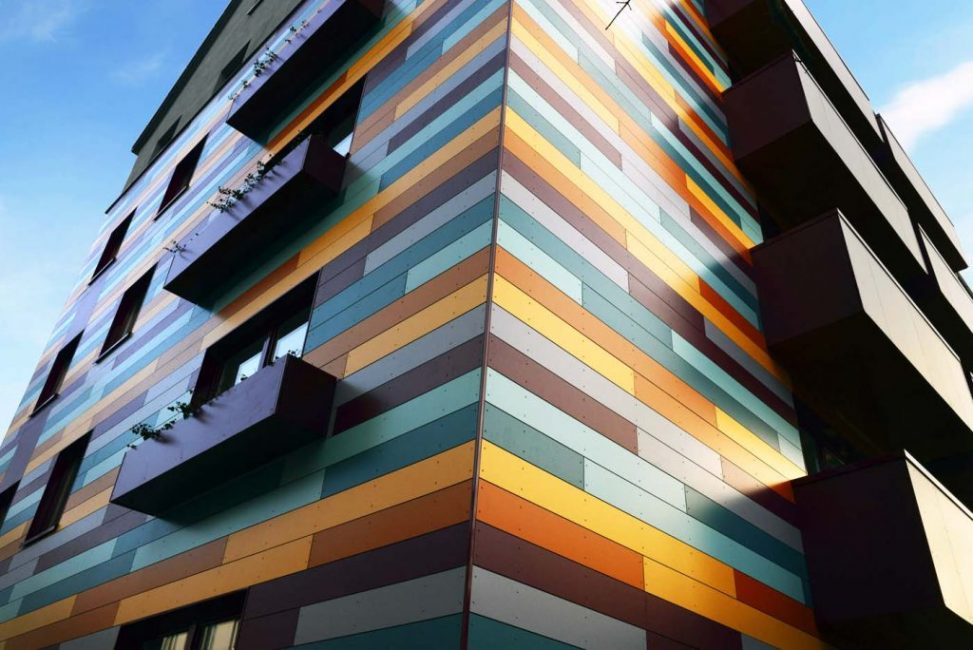
The final finishing result
Preparation for finishing window and door openings consists in dismantling the old shutters and mechanisms for raising the blinds. When installing plates around windows and doors, a frame of metal profiles is produced around their entire perimeter. Fastening is carried out with self-tapping screws, and the edges of the plates for docking are cut at an angle of 45 degrees.
The joints of the panels in the corners are carefully worked out with a sealant. Also, when finishing openings, a decorative metal profile is used, which is attached to a window or door frame. The joints of profiles and additional elements are treated with acrylic paint, matching the color of the panels.
The finished mounted facade does not require special care: if dirty, it can be washed with plain water. At the same time, the finish will not lose its decorative properties.
Holes from self-tapping screws are not recommended to be sealed with sealant: it will not be possible to paint them in the same color. Repair paint, putty or primer will help mask the fasteners.
Fiber cement panels are rarely used to finish the basement: the material can quickly collapse due to high levels of humidity. However, many manufacturers have taken this feature into account and have already launched panels with increased resistance to moisture.
Socle ebbs are installed at a height of 7–10 cm from the level of the blind area to protect the foundation of the building from excessive moisture. The bottom row of kleimers is installed directly above them.
![[Instruction] Do-it-yourself laminate on a wooden floor: a complete description of the process. Laying schemes, what materials should be used (Photo & Video) + Reviews](https://iherb.bedbugus.biz/wp-content/uploads/2018/05/laminat-300x200.jpg)
Manufacturers and prices
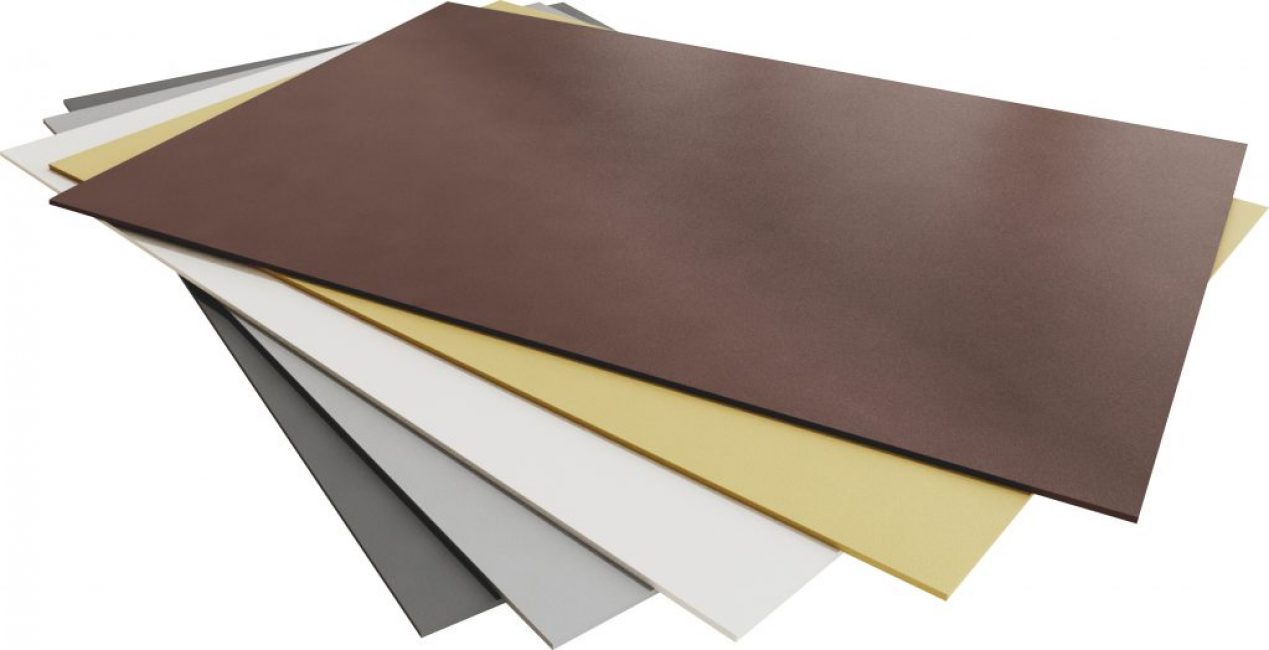
Japanese stoves
The main manufacturers of high-quality fiber cement boards in the world are Russia, Japan and Belgium, Finland, and Denmark.
Characteristics of building materials are presented in the table.
Manufacturer country | Firm | Peculiarities |
---|---|---|
Russia | Kraspan | The production of not only panels, but also fastening systems and additional elements has been established. |
Russia | Rospan | It produces sheets with a three-layer coating of various designs. The material has increased resistance to light, moisture, low temperatures. |
Russia | LTM | For facade cladding in regions with high humidity, the Aqua series of plates has been developed, there are windproof and fire-resistant panels. The service life of the composite reaches 100 years |
Russia | Latonite | The product line includes painted and unpainted pressed panels, as well as siding profiles. |
Belgium | Eternite | Products with a multi-layer coating are durable and resistant to frost. |
Japan | Nichiha | Wear resistance and service life of more than 50 years without repair |
Japan | KMEW | Plates of increased strength, with imitation of natural textures. They have the ability to self-clean: due to the presence of glass ceramics in the composition, dirt does not penetrate inside, but is washed away by rain |
Finland | Minerite | High-quality and frost-resistant plates in the middle price segment |
Denmark | Cembrit | Produces high quality panels |
Price
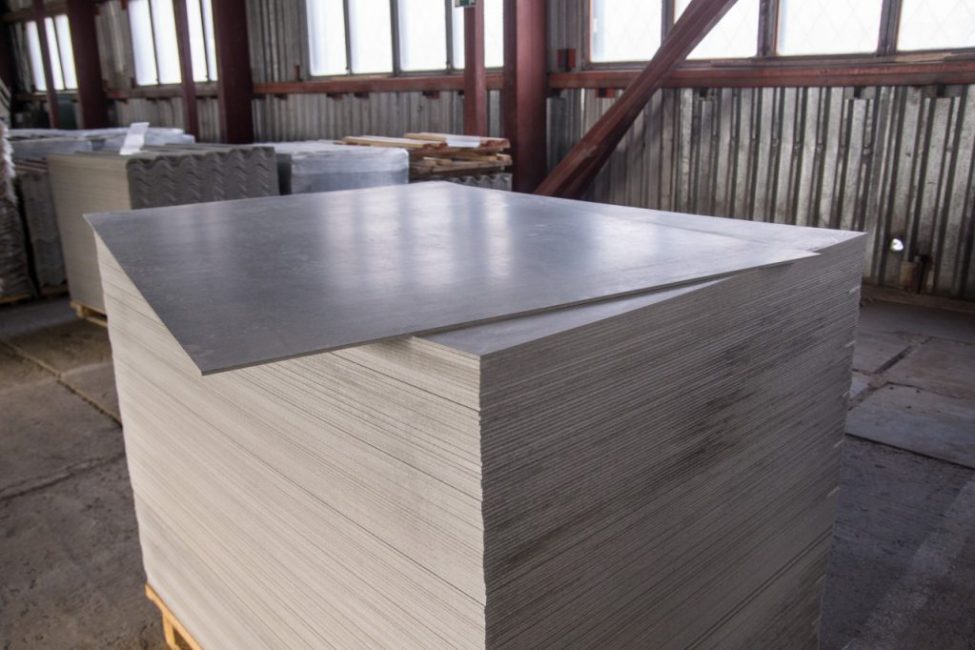
Finishing panels of Russian production
Japanese plates on average cost from 1600 rubles per square meter, the cost of European ones starts from 1000 rubles per 1 m2. Russian cladding panels will cost less: from 500 rubles per 1m2 from Rospan and from 900 rubles for the same area from Kraspan.
The cheapest composite facing boards are offered by manufacturers from China, Taiwan and Malaysia, but the quality of this material is also quite low.
The minimum cost of installation of the subsystem, insulation and fiber cement slabs is 1200–1500 rubles per 1 m2. The price of finishing is affected by the weight and thickness of the panels, the composition of the reinforcing fiber and the installation of additional fasteners.
Subsystem materials - crate and fastening cost 1500-1700 rubles per 1 m2, you may need a sealant, matching acrylic paint and additional fittings (the price for such an extra kit starts at 1000 rubles).
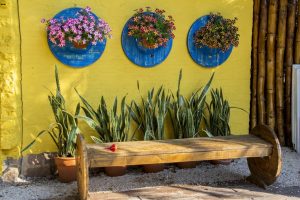
How to choose
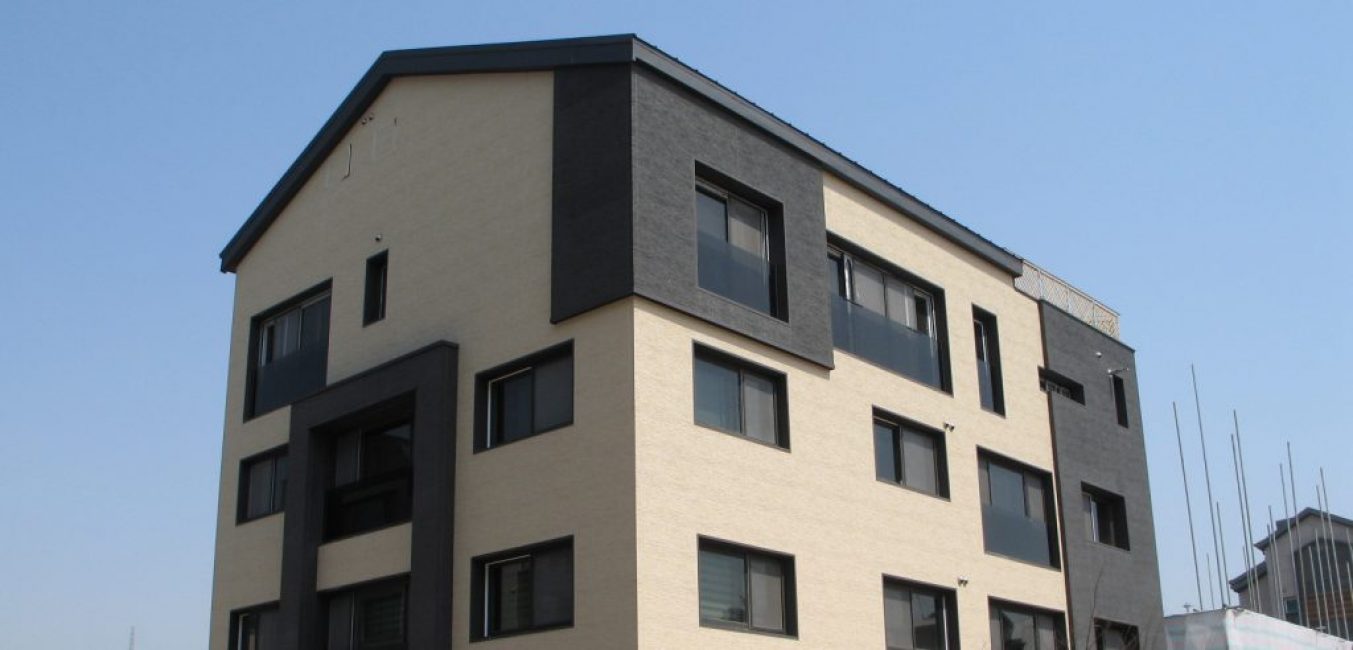
Composite finish
The standards of fiber cement panels from different manufacturers are defined in special documents: DIN EN 12467 and GOST 8747-88.
When choosing a high-quality finishing material made of concrete and synthetic fibers, it is recommended to pay attention to the following characteristics:
- Equipment. Suitable fittings and additional elements should be attached to the panels: profiles for collecting the sheathing and sleds, acrylic paint for processing cuts. Mounted plates are more profitable to purchase together with metal profiles and decorative panels
- Compound. Japanese manufacturers put an additional layer of glass-ceramic into the panels to protect against precipitation and UV radiation
- Same structure and uniform panel density.Before purchasing, you should carefully check the side ends of the plates so that they are of the same thickness along the entire length
- Weight. An important characteristic when carrying out installation work at height. Knowing this parameter will also give an idea of the amount of fasteners required.
- Fiber characteristics. KMEW panels use cellulose fibers, while Nichiha boards use hardwood chips.
- Mount type. Cleamer siding has no visible fasteners and looks more refined and more expensive.
- Front side paint quality. The appearance of the building and its aesthetic appeal depend on this.
Tthe thickness of the panels also plays an important role: the higher it is, the more fasteners are needed. With an indicator of 16 mm, clamps are used, for which special grooves are provided. Thicker slabs also help refine the texture of the finish.
When choosing the color and design of the panels, it is best to contact a specialized building market. If you choose a color scheme in an online store, you may end up disappointed, because the computer monitor distorts colors.
Exterior fiber cement panels are a great way to make a building look more attractive, insulate and protect it from fire, moisture and noise. The exceptional decorative and operational characteristics of the plates allow you to create a unique design of the building, and even a novice in installation work can install them.
The videos provide step-by-step instructions for installing fiber cement panels from different manufacturers:
Installation instructions for facade fiber cement panels
Fiber cement panels for exterior home decoration: high-quality cladding with unique properties (65+ Photos & Videos) + Reviews
Thermopan Facade panels
Fiber cement panels for exterior home decoration: high-quality cladding with unique properties (65+ Photos & Videos) + Reviews
The secrets of the correct crate are given in the video:
Crate for fiber cement siding. How to do it right? Installation secrets.
Fiber cement panels for exterior home decoration: high-quality cladding with unique properties (65+ Photos & Videos) + Reviews